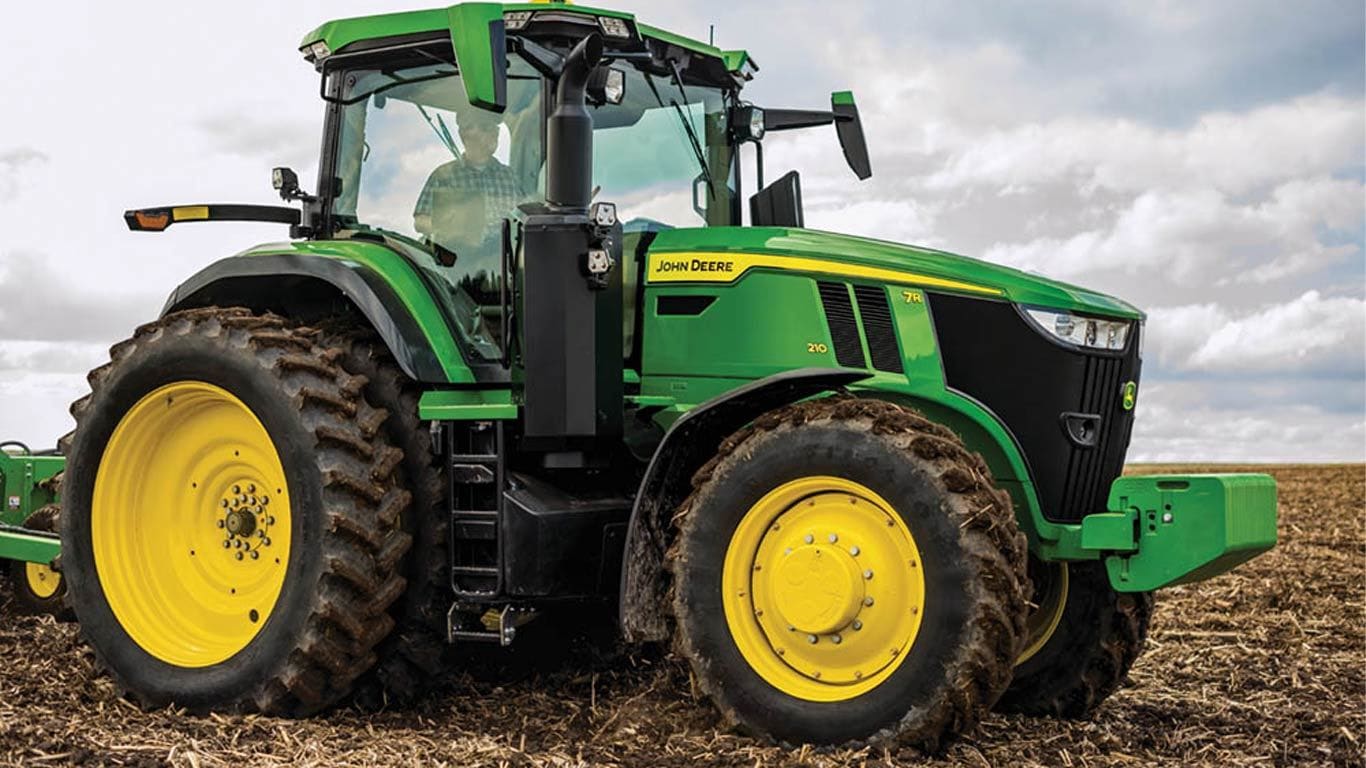
7R 210
Tractor
- Engine HP1: 231 Max | 210 hp Rated
- Fully integrated precision ag technology
- Choice of e23™ PowerShift or Infinitely Variable Transmission (IVT™)
- Three cab and visibility packages available to customize your tractor
- Industry-leading power transfer with Cat 4 HD drawbar for heavier implements
1Engine power PS (hp ISO) at max engine power speed (ECE-R120). John Deere Standard RES10080, SAE Standards J1995.
Request a Demo
Features
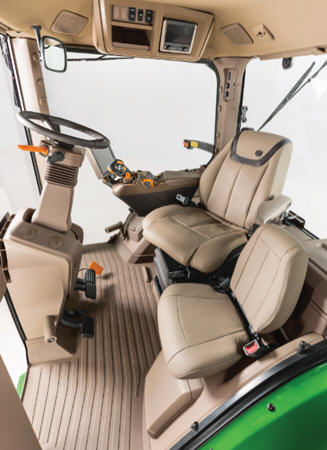
The Ultimate Comfort and Convenience package offers unsurpassed visibility, operator comfort, control placement, and ride and sound quality. Features in this package include:
Controls
- CommandARM™ console with hitch and hydraulic integrated controls
- Air conditioner and heater with automatic temperature controls
- Radio and volume controls
- Hitch control lever lock and selective control lever lock
- Tilt/telescoping steering wheel with position memory
- Auto trac resume button
- iTEC™ engagement buttons
Displays
- 21.3-cm (8.4-in.) 4200 or 26.4-cm (10.4-in.) 4600 Generation 4 CommandCenter™ Display
- Digital cornerpost display with:
- Fuel level gauge, including low fuel warning
- Temperature gauge
- Diesel exhaust fluid (DEF) gauge, including low DEF warning
- Engine rpm
- Transmission commanded gear or wheel speed
- Vehicle system functions, such as iTEC system, that are operating
- Monitor mounts on right-hand front post and rear cab post
Storage
- Storage compartment underneath the instructor seat
- Left-hand ceiling storage compartment
- Refrigerator located on the left side behind the instructor seat
- Beverage holders sized to accommodate various containers
Sound
- Passive noise reduction system
- Premium sound system, including touchscreen radio, smartphone interface, AM/FM/WX, aux and Bluetooth® wireless with voice control, inputs, XM® ready, six speakers with one subwoofer, and business band ready
Outlets
- Three 12-V convenience outlets (cigarette lighter style)
- Six 12-V three-pin outlets with adapter (provides switched and unswitched power)
- Four charging USB ports
- 120-V AC power outlet
- One International Organization for Standardization (ISO) nine-pin connector
- Service ADVISOR™ data port
Windows
- Swing-out rear window that opens 30 degrees
- Laminated glass
- Two-speed and intermittent front, rear, and right-hand side wiper with washer
- Front, left and right-hand side, and rear pull-down sunshade
Lights
- Interior dome light in the ceiling
- Map lights
For additional attachments and mounting solutions, see Cab convenience or Cab mounting solutions.
Seat
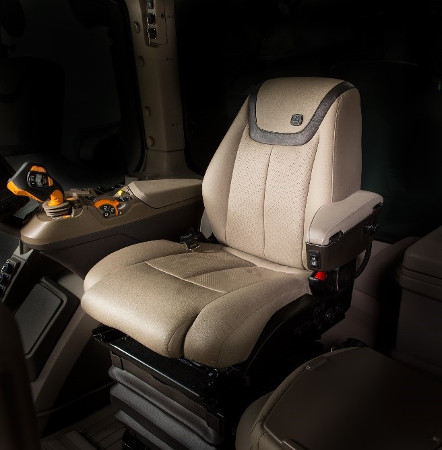
The seat improves ride quality and helps to reduce operator fatigue.
Features include:
- Leather
- Heat and ventilation to keep the operator at a comfortable temperature
- Adjustable bolsters
- Massage functionality
- Electronic controls to adjust to operator preference
- Pneumatic lumbar adjustment
- Seat height adjustments conveniently located below the left armrest
- Fore-aft adjustment is easy to reach, located below the left armrest
- Swivel adjustment, located on the front of the seat, allows the seat to be swiveled 40 degrees to the right or 25 degrees to the left of the center position with a pivoting CommandARM console
- Seat can be configured with air seat suspension, ActiveSeat™ II suspension, or air seat plus cab suspension
- Operator presence switch warns if the operator is out of the seat while operating key functions
- Seat belt retractor
- Centered cab seat provides excellent over-shoulder visibility
- Adjustable shock absorber permits ride adjustment from soft to firm to match the operator's desired comfort level
- Removable cushions allow for easy cleaning
- Folding instructional seat
Bluetooth is a trademark of Bluetooth SIG, Inc. XM is a trademark of Sirius XM Radio, Inc.
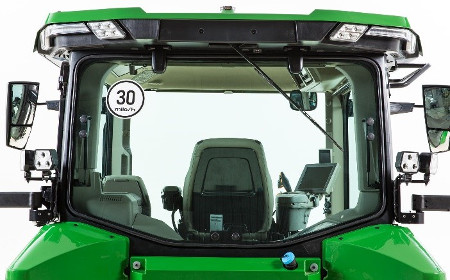
Visibility is one of the most important attributes of the cab. While lighting is a large portion of that, features like windshield wipers, mirrors, sunshades, and cameras are also important to overall visibility. For this reason, John Deere offers three visibility packages on 7 and 8 Series Tractors:
- Select
- Premium
- Ultimate
Lighting
The lighting configurations are available to match various applications and ensure maximum around-the-clock productivity.
Light housings are large, allowing for optimum total lumens and available light. The Select Visibility package uses 65-W halogen bulbs, whereas the Premium and Ultimate Visibility packages use light-emitting diode (LED) lights. The Premium and Ultimate Visibility packages replace Select Visibility package’s halogen lights with LED lights. The only lights that are not LED are the low-beam driving lights; they remain halogen. This allows each LED light to work at a lower temperature and no one light works harder than any other. The uniformity in LED coverage allows only one type of light output surrounding the tractor.
The lighting pattern in the Ultimate Visibility package provides industry-leading performance in nighttime visibility. LED lights provide maximum brightness and a true color output for excellent field definition that is easy on the operator's eyes.
The LED lights provide 40 percent greater coverage width and 10 percent more light coverage in the rear. LED lighting packages use 45 percent less amps than standard halogen lights and have an increased life expectancy over HID lights which leads to lower costs of ownership over the life of the tractor.
The low- and high-beam driving/work lights are adjustable. Please refer to the electrical section in the Operator’s Manual for complete details on adjusting lights.
NOTE: Lighting packages may vary depending on region.

The John Deere Active Seat II utilizes an electrical control system to control the vertical seat top movement. The "active" control system minimizes vertical seat top acceleration by sensing vertical tractor inputs and actively positioning the seat top to cancel those inputs. This results in a significantly smoother ride for the operator.
The John Deere ActiveSeat II has many of the same features of the air suspension seat with the addition of a ride firmness switch. The ride firmness switch is located on the left-hand armrest and replaces the suspension shock-dampening seat attenuation lever on the front right-hand side of the seat controls.
The ride firmness switch has three positions: plus, minus, and mid position. The three positions provide three different levels of seat performance:
- The plus position provides the greatest degree of ride firmness. This position allows more of the tractor's inputs to be felt by the operator (slightly rougher ride).
- The minus position provides the least degree of ride firmness, allowing minimal tractor inputs to reach the operator, resulting in maximum seat performance.
- The mid position allows a balance between the plus (+) and minus (-) settings.
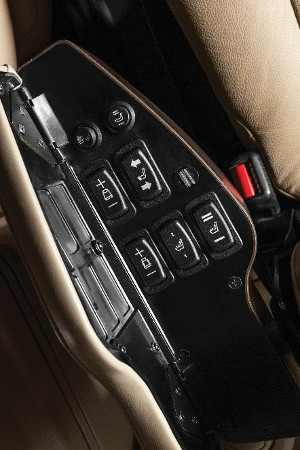
The ActiveSeat II is also available as a heated and ventilated leather seat for increased comfort and easier cleaning. This is only available with the Ultimate Comfort and Convenience package. For tractor applications where operating speed is not limited by the implement, the ActiveSeat II can allow for faster field speeds and increased overall comfort and productivity.
The leather seat includes massaging capability to alleviate operator fatigue.
Right-hand seat swivel has been improved above current 8R Tractors to 25 degrees (versus 8 degrees) to the left and 40 degrees to the right in the Premium and Ultimate Comfort and Convenience packages.
NOTE: The John Deere ActiveSeat II is not available on track tractors.
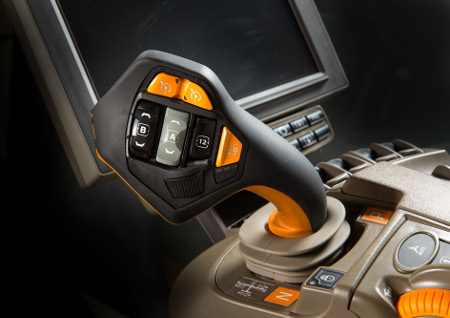
The unique driving strategy is designed to deliver highest performance in combination with operator comfort making the daily work much easier and efficient.
Driving strategy
- Pedal and joystick mode are active at the same time
- ActiveZero keeps the output speed actively at 0 km/h (0 mph) until command for acceleration is given independent of load or engine speed
- Command top and zero speed simply by one push or pull
- Unique inching control
- Three easily adjustable travel set speeds
- Two engine set speeds
- Three acceleration response settings
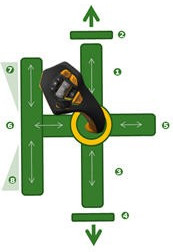
Forward movement | Reverse movement | |
1 | Accelerate | Decelerate |
2 | Top set speed | Zero speed |
3 | Decelerate | Accelerate |
4 | Zero speed | Accelerate |
5 | Activate set speed | |
6 | Select direction | |
7 | Inching speed | |
8 | Inching speed |
NOTE: The CommandPRO control is only available on IVT™ transmissions.
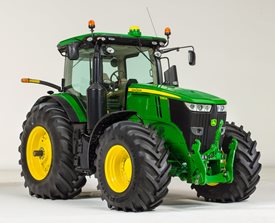
The optional TLS Plus is a fully integrated, self-leveling front suspension system available on 7R Tractors equipped with the 1300 mechanical front-wheel drive (MFWD) axle. TLS Plus provides exclusive front suspension using a hydro-pneumatic self-leveling system to increase productivity and improve ride dramatically. TLS Plus provides more control over the front suspension of the tractor.
TLS Plus increases both transport and field productivity with superior stability, ride, and comfort. Loader operators appreciate the enhanced performance when transporting bales or a full bucket of silage. In the field, the TLS Plus front suspension maintains ground-to-tire contact, enabling more power to the ground.
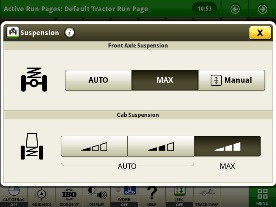
In the Generation 4 CommandCenter™ Display, the operator can select maximum pressure to accommodate for the transfer of heavy loads with minimal front axle movement.
The TLS Plus front axle is available with or without wet-disk front brakes. While TLS Plus is available on all 7R Tractors, it is a requirement for the following:
- 31 mph/50K e23™ transmission
- 31 mph/50K Infinitely Variable Transmission (IVT™)
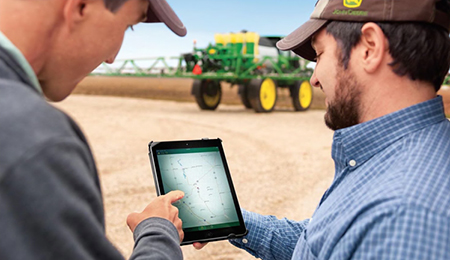
When you buy John Deere equipment, you expect reliability. You also know that problems can happen, and a product is only as good as the support behind it. That’s why John Deere equipment is prepared with technology that senses potential issues and can alert you and your dealer promptly—in the cab or anywhere you are.
John Deere Connected Support is a revolutionary change to support that leverages technology and the connectivity of JDLink™ telematics to prevent downtime and resolve problems faster. These tools decrease downtime by an average of 20 percent, enabling faster responses to unexpected problems and reducing technician trips to your machine. For some issues, unplanned downtime can even be prevented altogether through prediction of the issue.
With your permission, John Deere Connected Support:
- Keeps you running by monitoring machine health and promptly alerting you and your dealer of issues
- Saves time by remotely viewing in-cab displays, reducing trips to the machine
- Reduces or even eliminates technician trips to a machine through remote diagnostic and remote software reprogramming capabilities
- Connects experts with the information needed to respond to downtime faster and prevent it altogether
With more than a decade of experience leveraging connectivity to solve problems, no one else has the experience, tools, and knowledge to keep you running as John Deere and your John Deere dealer can. Connected Support is an in-base feature on all John Deere products with factory- or field-installed JDLink.
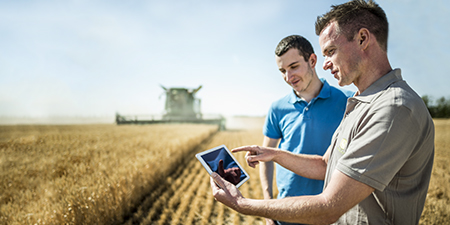
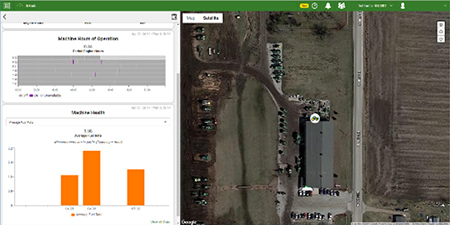
Producer needs and their success is John Deere’s focus. As functionality becomes more accepted and even expected, that functionality moves from being optional to being included with the machine. In model year 2019, AutoTrac™ guidance and documentation was included on machines equipped with a 4600 CommandCenter™ Display. Five years of JDLink is also included with the purchase of all model year 2020 and newer machines equipped with a 4G LTE Modular Telematics Gateway (MTG). The functionality of JDLink on these machines includes everything that was previously included with JDLink Access + Remote Display Access (RDA) and JDLink Connect subscriptions. This added connectivity enables customers to realize the value of a connected machine more easily.
- Easily transfer data and collaborate with trusted advisors to plan your field work quickly. You or your employees can spend more time in the field working rather than sitting on a headland setting up the technology. With a connection between John Deere Operations Center and your machines, changes to field plans occur as needed. Those changes may include changes in varieties, application rates, or machines.
- Better enable data-driven decisions. By using the insights gathered from machines along with the tools in Operations Center (e.g., Field Analyzer, Field Analyzer Beta, and Machine Analyzer) you can understand how your fields are performing and what field plans had an impact. John Deere Operations Center gives you access to more than 100 connected software tools, so you have the ultimate choice of popular industry tools. And, if you don't want to analyze the data yourself, you can share the data with those that help you make decisions to provide the insights you need.
- Report work completed accurately and timely for compliance and billing purposes.
- Increase machine uptime with Connected Support. Your local John Deere dealer can provide remote monitoring services and diagnostics to help keep your machines up and running, reduce your maintenance expenses through early detection of problems, and provide over-the-air software updates for displays, receivers, and controllers.
- Get quick in-field support with RDA. You can monitor your machines from your office computer or a mobile device on the go.
- Remotely manage machines and employees to give you insights into how they are performing. If machines are being underutilized or field operations are not being properly conducted, you can put plans in place to improve productivity.
- Quickly make changes to improve your harvesting operations by remotely viewing and adjusting combine settings.
To use JDLink, the following is required:
- MTG
- JDLink connectivity service
- A John Deere Operations Center account to access machine and agronomic data
The Generation 4 CommandCenter was designed to provide a consistent user experience by providing full screen viewing of more run page modules, shortcut keys, and precision agriculture capabilities.
Expect easier setup, along with increased operator confidence thanks to a simple, customizable interface. The improved design of the Generation 4 CommandCenter also aids in an optimal operating experience and maximizes uptime.
In order to increase your efficiency, take advantage of the following features offered by the Generation 4 CommandCenter:
Layout Manager
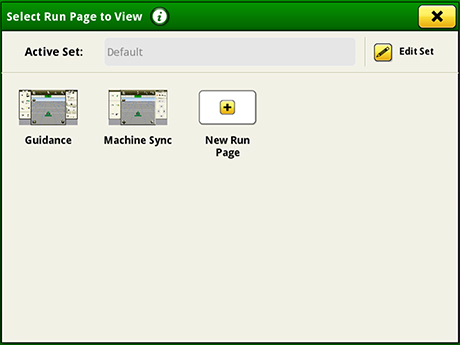
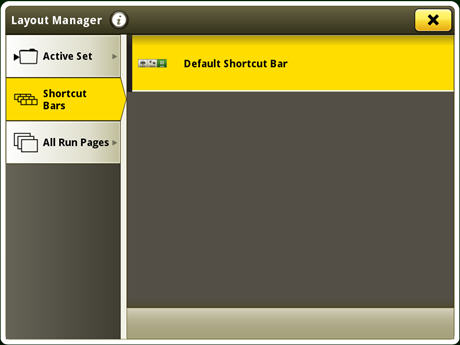
- Easily create page views that meet user needs and that are also equipped with default run pages.
Language and units
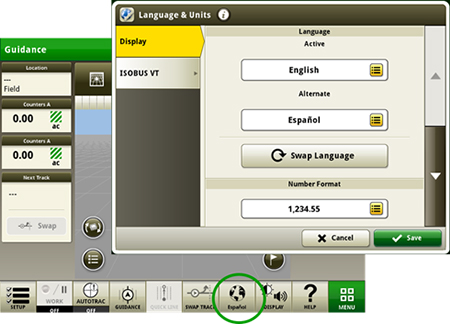
Easily switch between languages with the option to set the active and alternate language. Configure the shortcut bar to include the language toggle allows different individuals to easily switch the display between languages.
Users and access
Users and access allow the owner or manager to lock out certain functions to prevent operators from accessing or changing settings. Lock-out functions are managed with a defined pin for the administrator.
The Generation 4 CommandCenter can be set to one of two profiles, administrator or operator. The administrator profile is always set to the full access group. This group allows unlimited access to all the features and can lock and unlock features in the operator profile.
Machine Monitor
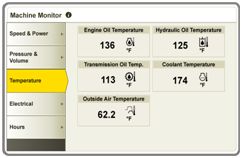
- The Machine Monitor application provides you instantaneous readings about the status or condition of your machine.
- This application shows parameters such as engine speed, coolant temperature, and ground speed.
Work Monitor
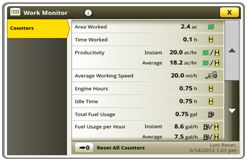
- The Work Monitor application displays performance information about the task being performed by the machine.
- You are shown averages, totals, and productivity of the machine, such as area worked, average working speed, and fuel usage.
- Work set up places the settings needed to properly setup features such as AutoTrac™ guidance, Documentation, and Section Control in a single location. Settings include:
- Client, farm, and field
- Crop type
- Machine and implement dimensions
- Variety/hybrid and planting/seeding rates
- Variable rate prescriptions
- Product and application rates
- Application rates through the implement screens
Operator's Manual
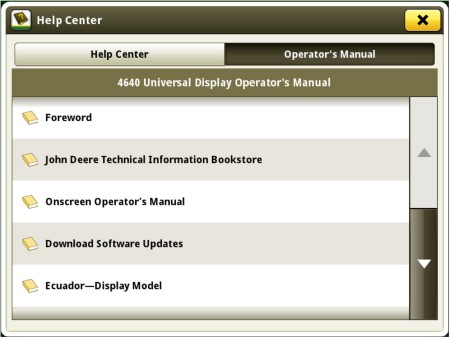
Stay up to date on the latest Gen 4 features and enhancements with the Gen 4 Operator’s Manual at the user’s fingertips. With each bundle update, the Gen 4 display automatically receives the latest Gen 4 Operator’s Manual which means less time locating a paper copy and ensuring the most up-to-date information is always available.
Video capability
The video application on 4600 CommandCenter and 4640 Universal Display has been redesigned to improve user interface and prepare for future enhancements. Features include the ability to name and configure cameras for viewing and scanning.
- Machines equipped with a 4200 CommandCenter are equipped with one video input, and the 4600 CommandCenter has four video inputs.
- You can set a variety of triggers. With each trigger, the image appears on the display.
Flags
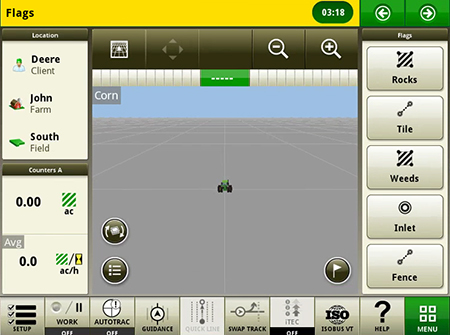
- Mark areas in the field that need special attention such as rocks, tile lines, or weed pressure.
- Flags previously recorded on the Gen 4 or GreenStar™ 3 2630 Display can be transferred between monitors.
- Flags previously recorded on the Gen 4 or GreenStar™ 3 2630 Display can be transferred between monitors.
Field boundaries
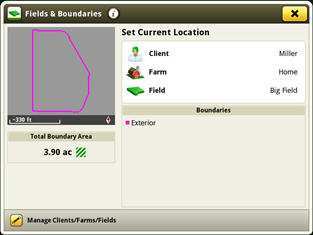
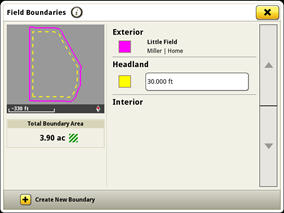
- Manually drive field boundaries with the Generation 4 CommandCenter or import existing boundary information from the GreenStar 3 2630 Display or John Deere Operations Center. Gen 4 documentation data can be used to create boundaries from coverage within the John Deere Operations Center.
Automatic base station switching
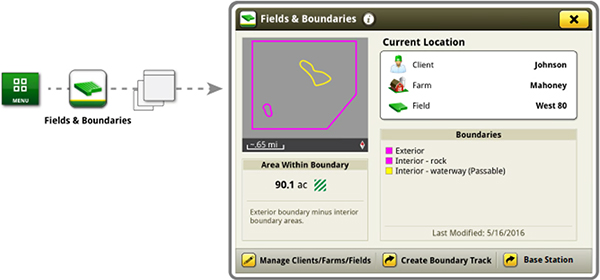
- Producers using John Deere RTK Radio 450 or 900 can link a base station to a desired client, farm, or field. This allows automatic switching to the associated base station when changing fields. The ability to import base station assignments into Operations Center and send back to machines will be available at a later date.
Dual-display mode
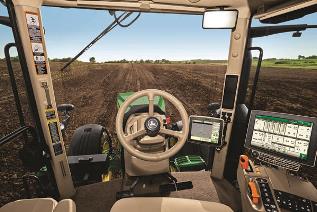
- Generation 4 CommandCenter may be configured to run with the following John Deere displays connected at the cornerpost of a John Deere tractor:
- GreenStar 2 1800 Display
- GreenStar 2 2600 Display
- GreenStar 3 2630 Display
- 4640 Universal Display
- 4240 Universal Display
NOTE: Vehicle applications are always located on the Gen 4 CommandCenter.
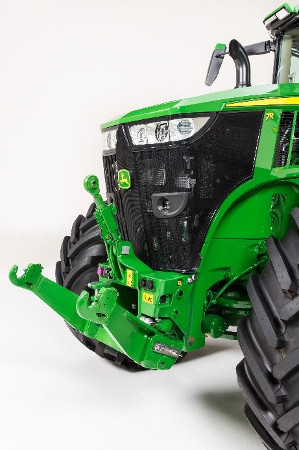
The 7R Tractors offer two front hitch options to best fit a variety of applications.
Standard (non-ground-engaging) hitch option for applications including, but not limited to:
- Front-mounted mowers, toppers, and snow blowers
- Carrying front seed hoppers and plow packers
- Carrying front ballast
- Operating light-draft implements
Premium (ground-engaging) hitch option for applications including, but not limited to:
- Operating primary tillage equipment and standard blades
Premium hitches include a push bar and heavier lift arms:
- Hitches with zero front auxiliary valves include one mid-mount valve.
- Hitches with one front auxiliary valve include two mid-mount valves.
- Hitches with two front auxiliary valves include three mid-mount valves.
To ensure adequate hydraulic availability, up to two selective control valves (SCVs) can be included with a front hitch.
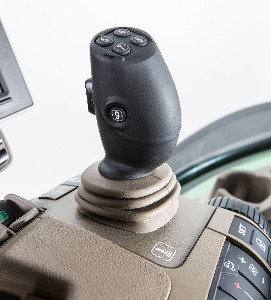
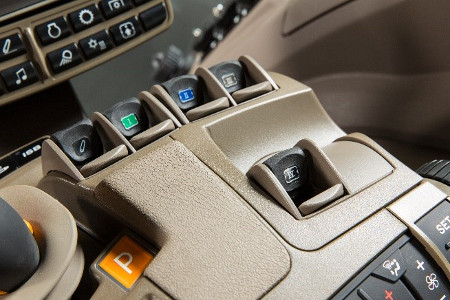
Tractors equipped with a factory front hitch have the option of selecting a joystick control or paddle pot SCV controls. The joystick control is not compatible with the sixth rear electrohydraulic SCV because of the CommandARM™ controls space required for the front hitch joystick.
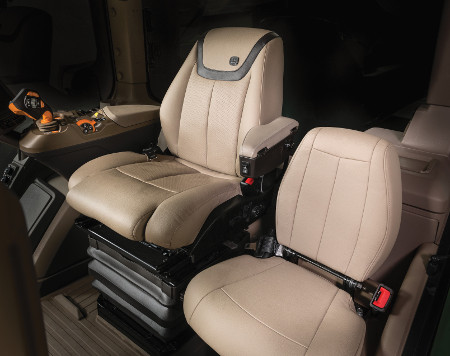
Comfort and Convenience packages
When you reach a 40-hour week by Wednesday, you're logging some serious hours in the cab. Spend that time in the refreshed and refined John Deere cab, and experience a quiet, comfortable ride with unrivaled visibility and convenience.
- Three package levels to fit your needs – Select, Premium, or Ultimate
- CommandARM™ console that puts everything you need within reach
- Plenty of storage
- Work comfortably during long days in the field with an automotive-style seat
- Keep electronics powered throughout the day with a variety of outlets
Comfort and Convenience packages | Select | Premium | Ultimate |
Seat |
|
|
|
Infotainment |
|
|
|
Business band ready | X | X | X |
Four USB and one 12-V outlet | X | X | X |
Dual tilt column | X | X | X |
Footrests | --- | X | X |
Refrigerator | --- | X | X |
120-V/300-W three-prong outlet | --- | X | X |
Carpeted floor mat | --- | --- | X |
Leather-wrapped steering wheel | --- | --- | X |
Bluetooth is a trademark of Bluetooth SIG, Inc. XM is a trademark of Sirius XM Radio Inc.
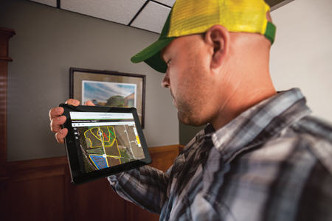
Your needs and success are the focus of John Deere. John Deere makes it easy for you to benefit from having a connected tractor in your operation. All tractors come standard with JDLink™ telematics system and users can turn on connectivity in the John Deere Operations Center™ application. With a StarFire™ Integrated Receiver and Generation 4 CommandCenter™ Display, you can easily step right into advanced technology. If you’re an advanced tech user, you’ll enjoy the benefits of a highly intelligent machine connected to a full suite of solutions on the most open platform in the industry. Advantages of a connected machine include:
- A StarFire Integrated Receiver eliminates all setup, installation, and global positioning system (GPS) calibrations
- AutoTrac™ assisted steering guides the machine with accuracy in a variety of field conditions
- Automation is an option with some applications
- John Deere Connected Support™ is a proactive service approach to improve service efficiency and reduce machine downtime
- JDLink gives you access to information anytime, anywhere, to make data driven decisions with John Deere Operations Center and Documentation
The technology and connectivity in John Deere tractors allow you to optimize productivity, increase uptime, and boost profits with machine information from any device, anywhere.
![]() |
![]() |
![]() |
StarFire Integrated Receiver | AutoTrac | JDLink |
Base equipment:
Optional equipment:
|
Base equipment:
Optional equipment:
|
Base equipment:
|
*Available with Premium Activation 3.0
**Available with Automation Activation 3.0
Specs & Compare
Key Specs | 7R 210 Current Model |
Engine description | John Deere PowerTech™ (B20 diesel compatible) 6.8L |
Engine displacement | 6.8 L 415 cu in. |
Rated engine power | ECE-R120: 154 kW 210 hp |
Maximum engine power | ECE-R120: 170 kW 231 hp |
Rated PTO power (hp SAE) | 126 kW 170 hp |
Maximum PTO power | |
Transmission type | Standard: John Deere e23™ 42 km/h 26 mph Optional: John Deere e23 transmission 50 km/h 31 mph John Deere Infinitely Variable Transmission (IVT™) 0.050-42 km/h (0.030-26 mph) John Deere Infinitely Variable Transmission (IVT) 0.050-50 km/h (0.030- 31 mph) |
Hydraulic pump rated output | Standard: 63 cc: 162 L/min 43 gpm Optional: 85 cc: 222.3 L/min 59 gpm |
Rear hitch category (SAE designation) | Standard: Category 3/3N with Quik-Coupler Optional: Category 3/3N with hook ends |
Base machine weight | e23, TLS™, 18.4R46: 10,000 kg 22,000 lb |
Maximum engine power PS (hp ISO) at max engine speed (EU 2016/1628) | |
Rated engine power PS (hp ISO) at rated engine speed (EU 2016/1628) | |
Engine specifications | |
Description | John Deere PowerTech™ (B20 diesel compatible) 6.8L |
Engine type | Diesel, in-line, 6-cylinder, wet-sleeve cylinder liners with four valves in head |
Engine family | MJDXL06.8309 |
Rated speed | 2100 rpm |
Aspiration | Single turbocharger, variable geometry turbo |
Cylinders liners | |
Emission level | Final Tier 4 |
After treatment type | Diesel oxidation catalyst (DOC)/diesel particulate filter (DPF) |
Displacement | 6.8 L 415 cu in. |
Engine performance | |
Rated power | ECE-R120: 154 kW 210 hp |
Rated PTO power (hp SAE) | 126 kW 170 hp |
Maximum PTO power | |
Intelligent Power Management (IPM) | |
Power boost | IPM: 23 kW 30 hp |
Maximum engine power | ECE-R120: 170 kW 231 hp |
Engine peak torque | At 1600 rpm: 983 Nm 725 lb-ft |
Drawbar power | |
PTO torque rise | 40 percent |
Fuel injection system and control | |
Air cleaner type | |
Maximum engine power PS (hp ISO) at max engine speed (EU 2016/1628) | |
Rated engine power PS (hp ISO) at rated engine speed (EU 2016/1628) | |
Transmission | |
Type | Standard: John Deere e23™ 42 km/h 26 mph Optional: John Deere e23™ Transmission 50 km/h 31 mph John Deere Infinitely Variable Transmission (IVT™) 0.050-42 km/h (0.030-26 mph) John Deere Infinitely Variable Transmission (IVT) 0.050-50 km/h (0.030- 31 mph) |
Reverser | |
Clutch; wet/dry | |
Creeper | |
Hydraulic system | |
Type | Closed-center, pressure/flow compensated system with load sensing |
Pump rated output | Standard: 63 cc: 162 L/min 43 gpm Optional: 85 cc: 222.3 L/min 59 gpm |
Available flow at a single rear SCV | 132 L/min 35 gpm |
Available flow at front SCVs | 126 L/min 33 gpm |
Number of rear selective control valves (SCVs) | Standard: four SCVs Optional: Three to six ISO couplers: 12.7 mm 1/2 in. Five ISO couplers (SCV 1: 19-mm [3/4-in.] couplers, SCV 2-5: 12.7-mm [1/2-in.] coupler) |
Number of mid selective control valves (SCVs) | |
Number of front selective control valves (SCVs) | One with front hitch |
Joystick SCV control | |
Auxiliary hydraulic features | |
SCV control | Electronic |
Rear hitch | |
Hitch draft control load sense type | |
Remote control valves available | |
Hitch category (SAE designation) | Standard: Category 3/3N with Quik-Coupler Optional: Category 3/3N with hook ends |
Maximum lift capacity behind lift points | Standard (Category 3): 5443 kg 12,000 lb Optional (Category 3N): 6894 kg 15,200 lb Standard (Category 3 with hook ends): 5443 kg Optional (Category 3 with hook ends): 6894 kg 15,000 lb |
Lift capacity at standard frame | |
Sensing type | Electrohydraulic |
Rear axle differential lock | |
Drawbar | |
Drawbar category | Standard: Category 3 Optional: Category 3 with heavy-duty support Category 4 |
Maximum vertical load | Standard: Category 3: 1,837 kg 4,050 lb Optional: Category 3 with heavy-duty support: 4,536 kg 10,000 lb |
Rear power take-off (PTO) | |
Type | Independent Standard: 44.45 mm (1.75 in.) 20-spline, 1,000 rpm Optional: 44.45 mm (1.75 in.), 20-spline, 1,000 rpm capable of 35 mm (1.375 in.) 540/1000 rpm 44.45 mm (1.75 in.) 20-spline, 1,000 rpm with 35 mm (1.375 in.) 540E/1000/1000E rpm gearcase 44.45 mm (1.75 in.) 20-spline, 1,000 rpm with 35 mm (1.375 in.) 540/540E/1000 rpm gearcase |
Engine rpm (at rated PTO speeds) | 540/1000 PTO rpm at 1950 engine rpm 540E/1000E PTO rpm at 1750 engine rpm |
Economy PTO speeds | |
Reverse PTO speeds | |
Multispeed PTO option availability | |
Ground speed PTO option availability | |
PTO actuation | Electric switch with adjustable modulation |
Front hitch | |
Category | Category 3N, ground engaging |
Electric power | Seven-pin connector |
Standard lift capacity | 5,200 kg 11,464 lb |
Front power take-off (PTO) | Available: 35 mm (1.375 in.) 21 spline, 1,000 rpm, counter-clockwise rotation (when facing PTO) Available through Parts: 44.45 mm (1.75 in.), 20 spline, 1,000 rpm, counter-clockwise rotation (when facing PTO) |
PTO speed | 1,000 PTO rpm at 1940 engine rpm |
Rear axle | |
Type | Standard: Rack-and-pinion or flange axles Optional: Diameter: 100 x 3010 mm 3.94 x 118.5 in. Diameter: 100 x 2808 mm 3.94 x 110.5 in. Diameter: 100 x 2550 mm 3.94 x 100.4 in. Flanged Axle: 335 mm 13.2 in. |
Final drive type | Inboard planetary three pinion |
Differential controls | |
Axle type | |
Brakes, type and control | |
Rear differential lock | Full-locking electrohydraulic |
Load rating | |
Front axle | |
Type | Standard: 1150 Series MFWD: tread range 1524 to 2235 mm 60 to 88 in. Optional: TLS: Tread range 1524 to 2235 mm TLS with front brakes available with 40 km/h 24.9 mph TLS with front brakes standard with 50 km/h 31 mph |
Front axle differential lock | 1150 Series MFWD: Limited slip TLS: Limited slip TLS with front brakes: Full-locking electrohydraulic (actuated at same time as rear diff lock) |
Load rating | |
Tires | |
Rear | RCI Group 47/48 |
Wheel tread range | |
Turning radius with brakes | 380/85R34 group 42 tires at 152.4-cm (60-in.) spacing 1300: 7 m 23 ft 600/70R30 group 43 tires at 188.2-cm (74.1-in.) spacing TLS: 6.7 m 22 ft |
Turning radius without brakes | |
Central Tire Inflation System (CTIS) | |
Front | |
Tracks | |
Tread spacing | |
Drive type | |
Track width | |
Mid-rollers | |
Steering | |
Brakes | |
Primary brake (foot brake) | |
Secondary brake | |
Park lock | |
MFWD braking | |
Front axle brakes | |
Auxiliary brakes | |
Hydraulic trailer brakes | |
Pneumatic trailer brakes | |
Electrical system | |
Alternator size | Standard: 210 amp Optional: 250 amp |
Battery options | 12 V |
Working lights | Standard: 18 halogen Available: 18 LED or 22 LED |
Type of bulb in headlight (Halogen, Zenon, LED) | Standard: 65-W halogen Available: LED |
Type of bulb in beacon (Halogen, Zenon, LED) | |
dB(A) rating for backup alarm | |
Total cold cranking amps | With two 925 CCA group 31 batteries: 1850 CCA |
Operator station | |
Rollover protective structure, OOS | |
Seat | Degree of seat swivel, left hand Optional: 25 degree Degree of seat swivel, right hand 40 degree Standard: air suspension Optional: ActiveSeat™ II |
Cab suspension | Optional |
Instructional seat | Standard |
Display | Standard: 4200 Generation 4 CommandCenter™: 17.8 cm 7 in. Optional: 4600 Generation 4 CommandCenter: 25.4 cm 10 in. |
Radio | Standard: AM/FM stereo with weatherband, remote controls, auxiliary input jack, four speakers and external antenna |
Inner cab volume | 3.24 m3 114 cu ft |
dB(A) rating | |
Cab glass area | 6.56 m2 70.61 sq ft |
Safety glass rating | |
Front visibility | |
Dimensions | |
Wheelbase | 2,925 mm 115.2 in. |
Overall width | |
Overall length | 5520 mm 217 in. |
Overall height | |
Drawbar clearance | Group 47 rear tires: 360 mm 14.2 in. Group 48 rear tires: 415 mm 16.3 in. |
Front axle center | |
Approximate shipping weight, Open;Cab | |
Weight | |
Base machine weight | e23, TLS, 18.4R46: 10,000 kg 23,000 lb |
Maximum ballast level | SAE PTO hp: 65.8 kg 145 lb |
Maximum permissible weight | |
Capacities | |
Crankcase oil volume | 26 L 6.9 U.S. gal. |
Fuel tank | e23™: 463 L 122 U.S. gal. IVT: 513 L 135 U.S. gal. |
Diesel exhaust fluid (DEF) tank | 26.2 L 6.9 U.S. gal. |
Cooling system | 39.5 L 10.4 U.S. gal. |
Transmission-hydraulic system | 160 L 42.3 U.S. gal. |
Serviceability | |
Interval for engine oil change | 500 hours |
Interval for hydraulic/transmission oil change | 1,500 hours |
Interval for engine coolant change | 6,000 hours |
Loaders | |
Loader | 700M |
Lift capacity at full height | 2417 kg 5304 lb |
Maximum lift height | 4741 mm 186 in. |
Leveling type | |
Precision AG | |
Guidance | Integrated AutoTrac™ |
Telematic | JDLink™ |
Remote diagnostics | ServiceADVISOR™ Remote: available with JDLink hardware and activations Remote Display Access: available with JDLink hardware and activations |
Miscellaneous | |
AutoTrac ready | |
ISOBUS ready | |
CommandCenter video inputs | |
Immobilizer | |
Side slope rating | |
Uphill/downhill slope rating | |
Country of manufacture | USA |
Additional information | |
Offers & Discounts
Accessories & Attachments
Cab Operator's Station
Cell phones, tablets, and other devices are key tools for farming today. John Deere has now made it easier than ever to incorporate these tools into the operator's station.
Stay connected with the RAM® cell phone and tablet mounts. John Deere offers a vast selection of adjustable accessory mounting solutions and media devices to fit every need and application.
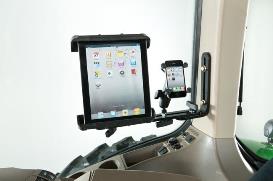
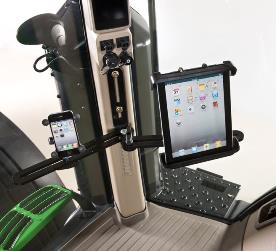
RAM is a trademark of National Products Inc.
Cell phones, tablets, and other devices are key tools for farming today. John Deere has now made it easier than ever to incorporate these tools into the operator's station.
Stay connected with the RAM® cell phone and tablet mounts. John Deere offers a vast selection of adjustable accessory mounting solutions and media devices to fit every need and application.
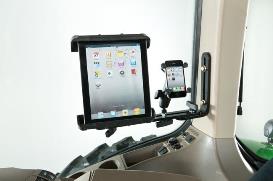
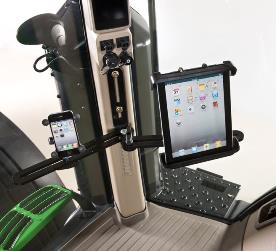
RAM is a trademark of National Products Inc.

Use the tables below to find all the parts needed to connect GreenStar displays physically and electronically.
For GreenStar 2 CommandCenter™ 2600/GreenStar 3 2630 Displays:
Mounting style |
Display mount (ball) |
Tie-rod assembly |
Rail mount (ball) |
Clamp |
PF11019 plus two 19M8648 |
RE574454 |
AXE59372 |
10-mm (0.4-in.) threaded |
PF11019 plus two 19M8648 |
PF80459 |
RE576490 |
|
|||
Single location bracket |
RE558242 |
The clamp-style mount with GreenStar monitor is not recommended with the vertical rail (BRE10575).
NOTE: Also order power harness (PF90686) and Ethernet cable (PFP12950). Optional protective film for screen (PF90596) is also available.
For 4240 /4640 Universal Display and Extended Monitor:
Mounting style |
Display mount (ball) |
Tie-rod assembly |
Rail mount (ball) |
Clamp |
AL212683 plus four 19M8648 |
AXE59372 |
|
10-mm (0.4-in.) threaded |
UC17356 plus four 19M8648 |
PF80459 |
RE576490 |
|
|||
Single location bracket |
RE558242 |
The clamp-style mount with GreenStar monitor is not recommended with the vertical rail (BRE10575).
NOTE: Also order power harness (PFP12435) and Ethernet cable (RE573617). Optional protective film for screen (PF90596) is also available.
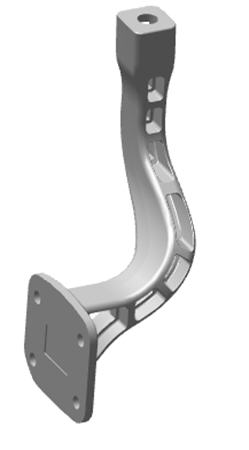
This unique bracket connects to the right side of the CommandARM. It is compatible with the cell phone mount (BRE10015), tablet mount (BRE10255), and more. It is also compatible with the touchscreen radio relocation kit (BXX11045) for Premium and Ultimate Comfort and Convenience packages.
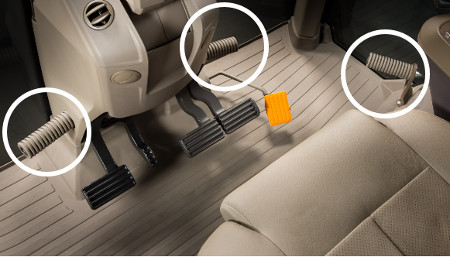
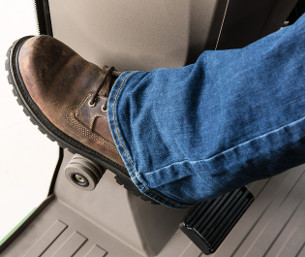
The steering column is designed to accept foot pegs, which are included in the Premium and Ultimate Comfort and Convenience packages. Producers with a Select cab can still easily add this feature.
The kit contains three pegs. Two front-facing pegs thread directly into the steering column. A third peg mounts near the right-side window and is used in combination with the right front peg when the operator seat is swiveled to the right. This upgrade is helpful when operating on steep downhill grades, sidehills, or watching towed implements.
Features:
- Direct bolt-on factory finish – no drilling or cutting required
- Heavy gauge steel to support any operator
- Color-matched rubber surfaces for comfort and vibration reduction
- Model year 2022 and newer are compatible with the extension and adjustment kit (BRE10511)
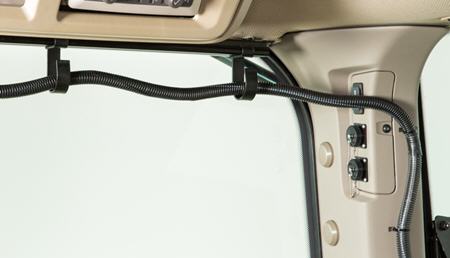
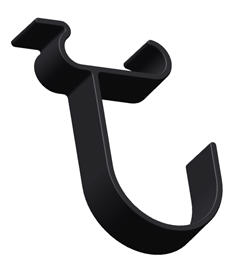
Keep accessory and monitor wiring neatly contained with these moveable harness hooks. These hooks are specifically designed to easily snap into the factory headliner rail and BRE10574 window mounting bracket and rail with no tools and can be moved as needed. These hooks allow accessory wiring to routed together for a clean look and maximized visibility.
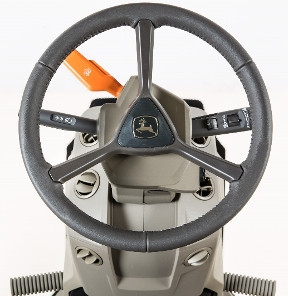
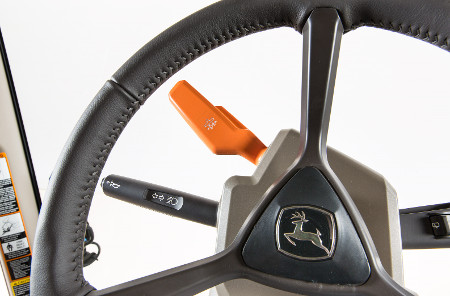
Add a little comfort to the day with the leather-wrapped steering wheel. This upgrade is included with the Ultimate Comfort and Convenience package and can be added to the Select or Premium cab by reusing existing mounting hardware.
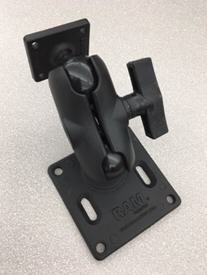
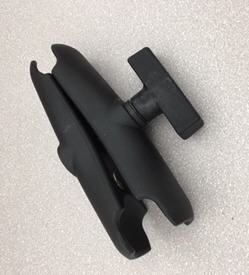
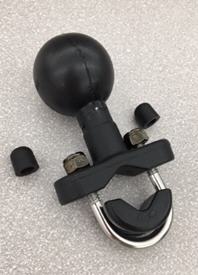
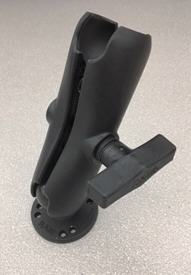

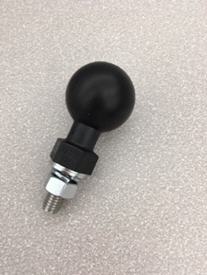
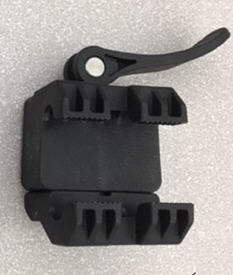
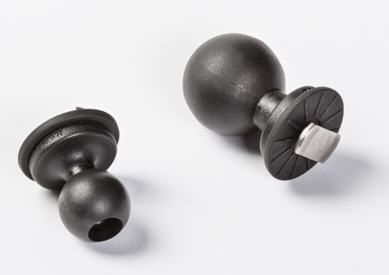
There are a variety of additional mounting part solutions available through John Deere to resolve unique mounting configuration needs. The table below includes several additional parts (not shown above) to aid in many different mounting needs.

Use the tables below to find all the parts needed to connect GreenStar displays physically and electronically.
For GreenStar 2 CommandCenter™ 2600/GreenStar 3 2630 Displays:
Mounting style |
Display mount (ball) |
Tie-rod assembly |
Rail mount (ball) |
Clamp |
PF11019 plus two 19M8648 |
RE574454 |
AXE59372 |
10-mm (0.4-in.) threaded |
PF11019 plus two 19M8648 |
PF80459 |
RE576490 |
|
|||
Single location bracket |
RE558242 |
The clamp-style mount with GreenStar monitor is not recommended with the vertical rail (BRE10575).
NOTE: Also order power harness (PF90686) and Ethernet cable (PFP12950). Optional protective film for screen (PF90596) is also available.
For 4240 /4640 Universal Display and Extended Monitor:
Mounting style |
Display mount (ball) |
Tie-rod assembly |
Rail mount (ball) |
Clamp |
AL212683 plus four 19M8648 |
AXE59372 |
|
10-mm (0.4-in.) threaded |
UC17356 plus four 19M8648 |
PF80459 |
RE576490 |
|
|||
Single location bracket |
RE558242 |
The clamp-style mount with GreenStar monitor is not recommended with the vertical rail (BRE10575).
NOTE: Also order power harness (PFP12435) and Ethernet cable (RE573617). Optional protective film for screen (PF90596) is also available.
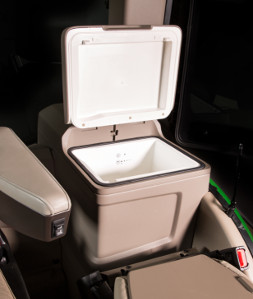
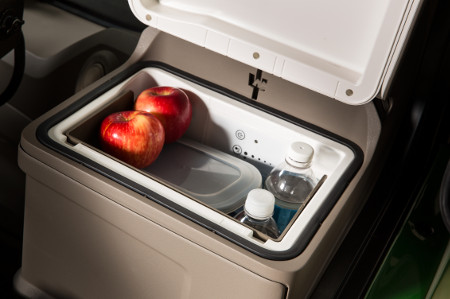
The refrigerator unit can be added to a cab ordered with a Select Comfort and Convenience package by purchasing the three service parts used in the Premium and Ultimate Comfort and Convenience packages. The main refrigerator unit installs inside the storage compartment behind the instructional seat and requires a weather seal and plug to be added. All wiring already exists, and no software is required to complete the install.

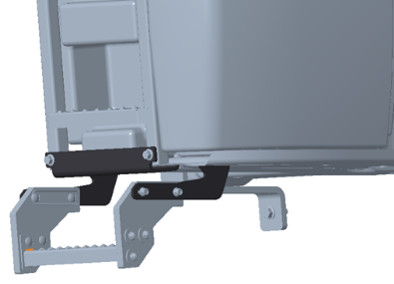
The lower step on the right side of the tractor, which is suspended with a flexible material, can be moved outward to gain easier access to the fixed-position steps. Making this adjustment means replacing the factory-installed mounting bracket with the bracket in this kit and reusing all the other parts.
This relocation is beneficial for operators with duals or who prefer a little extra space away from the tractor on the lowest step.
Adding this kit will change the overall width of some tractor models. Check local regulations for road width restrictions and permits as necessary.
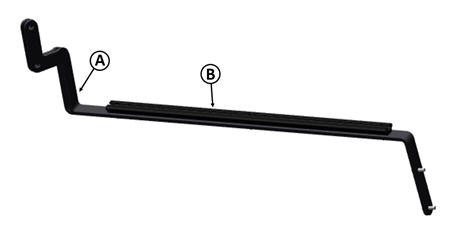
A large steel bracket, which spans the entire right-side window, mounts directly to the cab frame for rigidity and strength. The headliner mounting rail (included in this kit) is bolted to the steel bracket. This solution enables the operator to configure and reconfigure monitors and accessories without changing mounting solutions from either location. This rail accommodates clamp-style and T-slot style mount solutions (purchased separately).
- Spans the entire right-side window.
- Uses the same factory headliner mounting rail part number (R558980) for easy reconfiguring of accessories.
- Aluminum mounting rail mounts to either the top or underside of the steel bracket, allowing even more options and maximizing visibility preferences.
- Compatible with AXE59372 (clamp-style mount) and BRE10482 and BRE10483 (T-slot ball mounts).
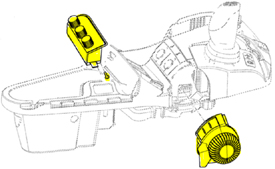
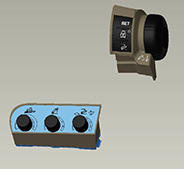
This kit provides additional (premium upgrade) controls for operating the rear hitch from the operator's seat.
A favorite worldwide, the RAM self-leveling cup holder is now available as a kit - designed specifically for Deere equipment. It is easily installed to keep your favorite beverage upright even in the roughest terrain. The perfect accessory for any cab that has 10-mm mounting bosses.
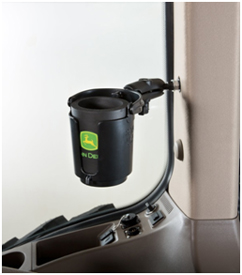

The new cup holder features a unique self-leveling design. This pivoting design allows easy adjustment for the holder while offsetting motion of the vehicle when moving.
Features and applications:
- Self-leveling action reduces spills
- Durable design for rough environments
- Easy adjustable mounting for ideal placement
- Includes John Deere branded beverage insulator
- Compatible with most monitor brackets and all 10-mm threaded bosses
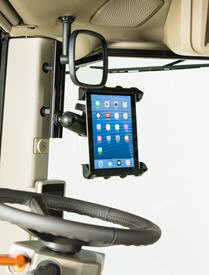

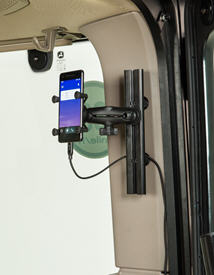
A shorter, 260-mm (10.25-in.) aluminum mounting rail is available. The kit includes all the hardware needed to mount in up to five vertical locations, including upper and lower right-side A-post rollover protective structure (ROPS), upper right-side C-post ROPS, and upper left rear C-post ROPS. It is compatible with both clamp-style and t-slotted ball mounts (purchased separately).
- Up to five vertical locations supported with this one rail (kit contains one rail and mounting hardware).
- Uses the same factory headliner mounting rail shape for ease of operator adjustment and preferences.
- Works in combination with other accessory bracket solutions.
- Compatible with AXE59372 (clamp-style mount) and BRE10482 and BRE10483 (T-slot ball mounts).
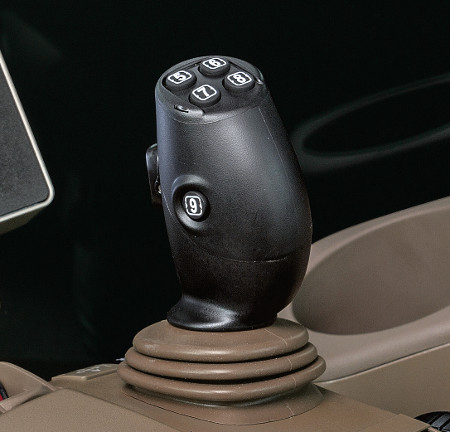
This optional cross-gate joystick (multifunction lever) replaces fingertip paddle pots for control of selective control valves (SCVs) and allows for programmable hydraulic functionality according to operator preference. It mounts directly to the CommandARM™ console. This is the same joystick (multifunction lever) that is included with a factory-ordered front-end loader.
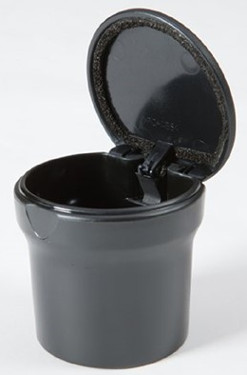
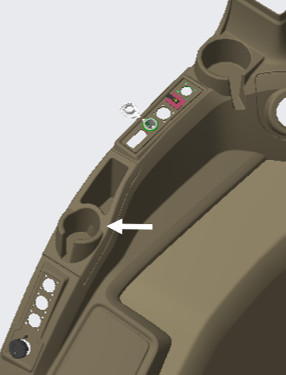
This storage container is a heavy plastic cup with a hinged lid and foam seal. It keeps ash, snacks, or small items well contained and fits snugly into the smaller cup holder in the upholstery (shown with arrow above) along the right-side window.
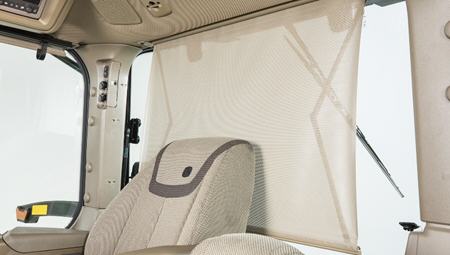
The cab uses the same sun shade part number in the front, right-side, and rear windows, which are included in the Premium and Ultimate Comfort and Convenience packages. Producers with a Select cab can easily add a sun shade or two.
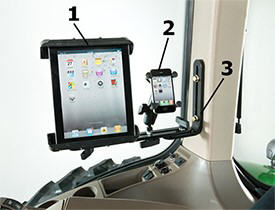
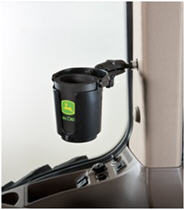
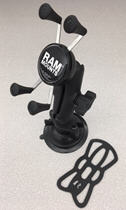
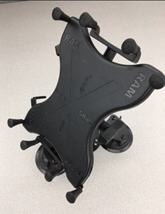
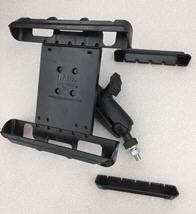

Mounting a tablet, cell phone, or beverage can be easily done with these solutions. These strong and simple-to-use solutions keep all important items right where they are wanted.
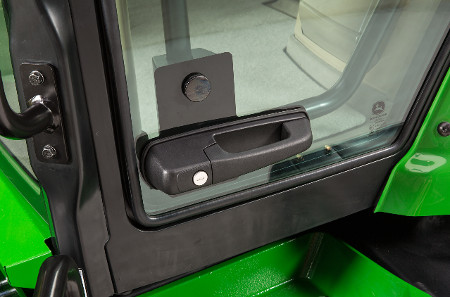
Add a level of security with this custom door lock handle. This kit replaces the factory-installed handle with a lock cylinder that is different from the ignition start switch and includes two matched keys. Additional keys must be made at a local locksmith.
Connectivity Hardware
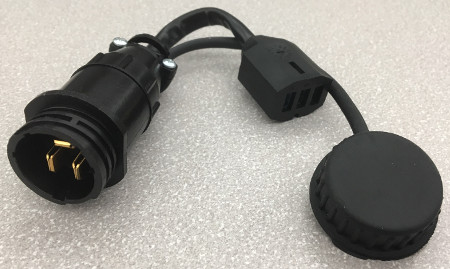
This adapter allows users to connect an amp-style, three-socket connector to the John Deere-style power strip connection type. Use this adapter to quickly and easily connect amp-style power accessories to older, vintage tractors that do not have an amp-style outlet already in the cab without cutting wire harnesses. This adapter can be kept connected into the John Deere-style power strip if users are regularly moving a unique display between vintage and newer tractors in the fleet.
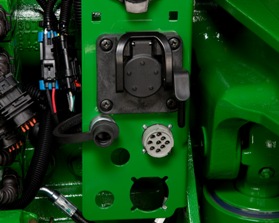
The nine-pin electrical connector is required to allow TouchSet™ depth control to be used with implements with this feature. The harness provides a position input to the tractor selective control valve (SCV) unit, enabling the TouchSet system.
This feature allows the operator to adjust height and depth of remote lift cylinders by using the TouchSet controls in the cab.
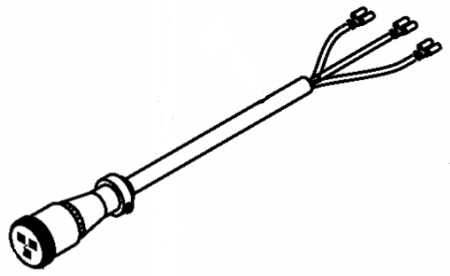
This adapter allows users to connect aftermarket displays to the universal amp power connector. The female three-socket connector has three flying leads that can be fused to the display harness. Once installed, the display harness will connect to the three-prong amp power adapter in the cab or to the RE67015 outlet adapter.
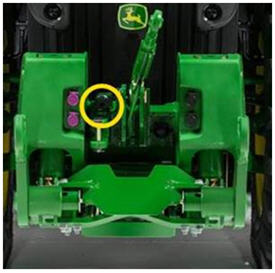
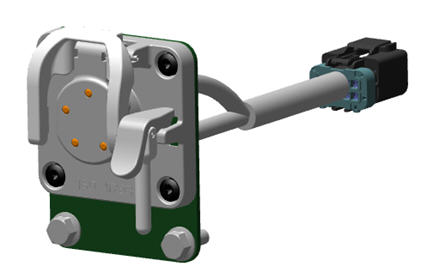
This kit allows any ISO-designed implement to transmit data to the tractor and back. It provides a controller area network (CAN) communication connection for front hitch ISOBUS implements.
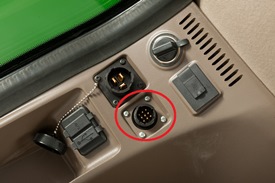
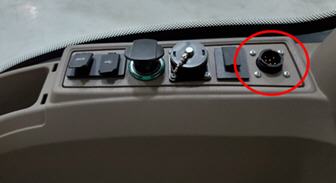
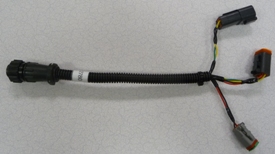
The ISO cab implement CAN bus adapter is available to connect any ISO compliant implement or device to an 8R, 8RT, 9R, 9RT, and 9RX (including Scraper Special) Tractor. These connectors are commonly used for planter frame control boxes.
Refer to the operator's manual, sections 16 (CommandCenter™) and 25 (Operator Station), for additional information on ISO implements.
NOTE: If the harness is not in use, unplug it from the ISO 11783 location or plug the four-pin connectors together on the harness. If neither of these are done, implement CAN communication errors occur.
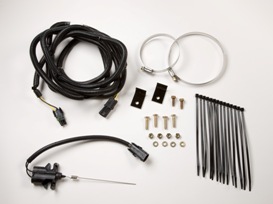
The implement switch indicates to the CommandCenter™ system when the implement is raised or lowered, providing accurate data collection when using a performance monitor.
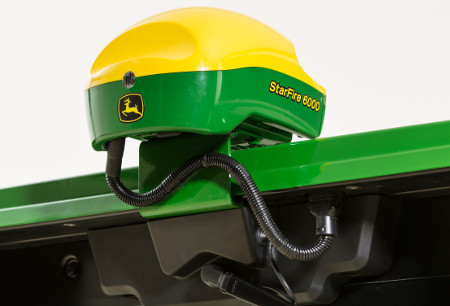
The model year 2020 and newer large tractors (with updated cab) have a low-profile, offset StarFire receiver integrated into the roof shell. However, there is a mounting bracket solution to add a StarFire 3000 (with deluxe shroud) or StarFire 6000 Receiver. This bracket connects to the center of the front roof near the wiper motor for an exceptional fit with a clean look. The 12-pin wiring harness on both the StarFire 3000 and StarFire 6000 are compatible with the base cab electrical connector.
DISPLAY HARDWARE
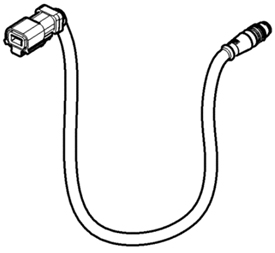
This cable connects the cornerpost Ethernet connector (square) to the GreenStar™ 3 2630 Display Ethernet connector (round). It is required for used with Remote Display Access (RDA), Wireless Data Transfer (WDT), and Machine Sync.
The square-to-round connector cable is 80-cm (31.5-in.) long.
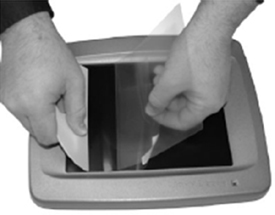
This product is similar to the protective film used on hand-held touchscreen electronics and can reduce screen damage from regular use. It includes all necessary instructions and tools to install the transparent film over a touchscreen display.
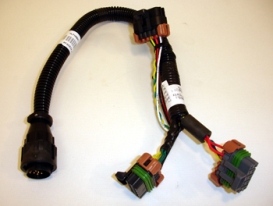
Drawbar

The 7R Series Tractor comes with a Category 3 adjustable swinging drawbar with pin and clevis. The Category 3 drawbar is also available with the clevis and heavy-duty support.
The Category 3 drawbar with heavy-duty support has a vertical load capacity up to 4536 kg (10,000 lb). This high vertical load drawbar is ideal for applications such as large-capacity grain carts and slurry wagons.
All drawbar options provide an easy-to-use linkage that allows the drawbar pin to drop into the field position when hooking up to an implement. This linkage is activated when it is tapped by the implement drawbar.

The 7R Series Tractor comes with a Category 3 adjustable swinging drawbar with pin and clevis. The Category 3 drawbar is also available with the clevis and heavy-duty support.
The Category 3 drawbar with heavy-duty support has a vertical load capacity up to 4536 kg (10,000 lb). This high vertical load drawbar is ideal for applications such as large-capacity grain carts and slurry wagons.
All drawbar options provide an easy-to-use linkage that allows the drawbar pin to drop into the field position when hooking up to an implement. This linkage is activated when it is tapped by the implement drawbar.

The 7R Series Tractor comes with a Category 3 adjustable swinging drawbar with pin and clevis. The Category 3 drawbar is also available with the clevis and heavy-duty support.
The Category 3 drawbar with heavy-duty support has a vertical load capacity up to 4536 kg (10,000 lb). This high vertical load drawbar is ideal for applications such as large-capacity grain carts and slurry wagons.
All drawbar options provide an easy-to-use linkage that allows the drawbar pin to drop into the field position when hooking up to an implement. This linkage is activated when it is tapped by the implement drawbar.
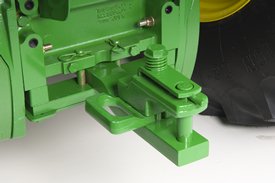
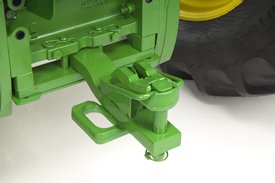
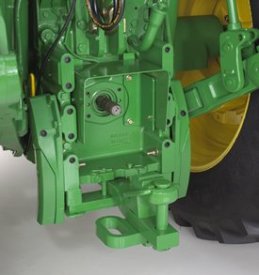
This drawbar clevis allows attaching implements equipped with a flat hitch link.
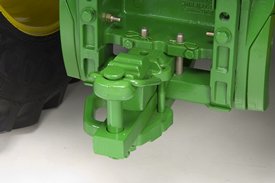
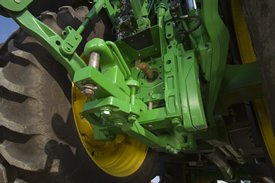
High vertical load drawbar improves tractor versatility by being compatible with implements with high hitch vertical loads.
This Category 3 drawbar option includes a heavy-duty drawbar support with maximum drawbar static vertical load at 4536-kg (10,000 lb) and can be adjusted to 25.4-, 35.6-, and 40.6-cm (10-, 14-, and 16-in.) lengths required by power take-off (PTO) implements. Drawbar pin size is 38-mm (1.5 in.).
Applications:
Medium- to heavy-sized 3-point-hitch implements, such as row-crop cultivators, and typical- to heavy-sized drawn field implements such as a field cultivator, chisel plow, or loaded grain carts.
Electrical
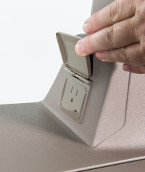
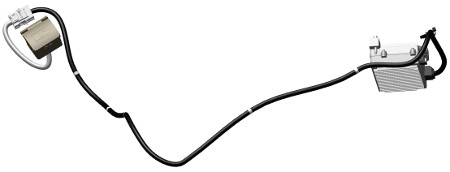
These kits include an inverter module, wiring harness, and interior color-matched receptacle. The mounting location is at the left C-post interior above the storage compartment or refrigerator unit. This inverter allows an operator to utilize household powered items such as a laptop or power tool charger. The receptacle kits are specific for either type B (compatible with type A and B plugs) or type C style socket (compatible with type C plugs). An interior, color-matched, self-closing cover is included to keep the socket clean from debris when not in use. This same feature is found in Premium and Ultimate Comfort and Convenience packages. Software is not necessary for this update.

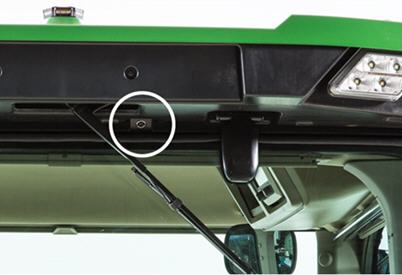
Increase visibility in the front, rear, or both areas of the tractor with a video camera system upgrade. If a Select or Premium Visibility package was ordered from the factory, producers can still upgrade to a front and/or rear video camera by simply purchasing the camera parts and mounting bezels.
The front camera mounts into the grill, and the rear camera mounts above the rear window in the roof assembly. These video cameras are a direct harness plug-in and do not require a software update. Video feed comes through the display on the CommandARM™ console.
Engine
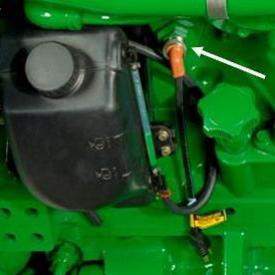
The optional cold start package is recommended for tractors frequently started at or below -6°C (21.2°F).
The kit includes a factory-installed activation switch and ether valve with ether canister. A 120-V, high-wattage block heater and grounded cord are also included with the factory-installed option.
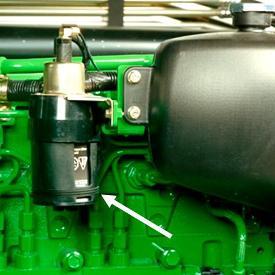
The engine ether kit is recommended for tractors frequently started in cold weather. This kit injects ether into the engine, allowing quick combustion in below-average temperatures.
IPM
NOTE: IPM is only available for Final Tier 4 (FT4)/Stage V engines, and not for Stage II and Tier 3/Stage IIIA engines.
This feature is for many typical farming operations that use the rear power take-off (PTO) in high-power applications or the tractor as a transport vehicle. Operators who are looking for more power in non-stationary PTO and transport applications will be interested in the IPM feature.
In high rear PTO power applications such as forage harvesters, rototillers, and beet or potato harvesting equipment or where heavy trailers, carts, or implements are moved to and from various locations, this feature provides significant additional capabilities. The solution improves productivity with more consistent ground speeds, quicker acceleration, and the ability to better hold desired transport speeds.
This two-in-one tractor solution successfully operates in power-intensive PTO and transport applications without being disadvantaged by the extra costs of the next higher horsepower model.
This feature is available as a factory- or field-installed option.
Tractor applications
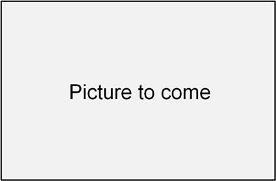
Rear PTO field applications
- Rear-mounted snow blowers
- Sugar beet harvesting
- Forage harvesters
- Potato harvesting
- Rotary cutters
- Mower conditioners
- Flail mowers
- Balers
- Soil stabilizing
- Power harrow
- Vegetable bed formers
- Muck spreaders
Transport applications
- Grain carts or wagons
- Slurry tanks
- Implement transport from field to field
- Pull-type sprayers
- Extensive operation in hills/roadways
This is not intended to be an inclusive list of all applications but shows the wide range of uses for additional engine horsepower.
Power available
IPM provides a controlled power boost of up to 26 engine kW (35 engine hp) to the tractor under the following operating conditions:
- Tractor moving and PTO under load
- Transport during acceleration
Power increase is not provided under draft applications or non-moving rear PTO applications.
How it works
There are specific operating parameters when IPM functions to boost engine power. It is the "intelligent" part of the system that provides seamless operation while adjusting the engine horsepower limits depending on how the tractor is being used. For engine horsepower boost activation, the tractor must be running an application that is using the full power capability of the tractor.
PTO activation
Power must be sensed going through the PTO by the tractor's electronic systems. The tractor must be moving at least 0.5 km/h (0.3 mph) and PTO consuming moderate power before power boost is enabled.
NOTE: If the tractor is equipped with a front PTO, additional IPM power may transfer through the front PTO. However, IPM activation is only sensed through the rear PTO. Adequate load must be sensed on the rear PTO for IPM to activate (non-transport work).
Transport activation
When in transport applications, power transition is smooth. The engine will respond seamlessly as load changes, such as when going up and down hills. Additional power is available at a useful transport speed with minor differences between tractor models and transmissions.
The minimum ground speed is where additional power will begin to be applied, assuming the engine is already fully loaded. Ramp up to full additional power occurs as speed continues to increase. Full additional power occurs within a 3 mph (5 km/h) band.
Transport during acceleration: power boost increases from 23 km/h – 28 km/h (14.3 mph – 17.4 mph).
Transport during deceleration: power boost decrease from 23 km/h – 18 km/h (14.3 mph – 11.2 mph).
Power boost levels other than at rated rpm
Power boost is a function of engine speed per the following example:

IPM (shown in red in chart above versus standard power shown in blue) provides additional engine horsepower from rated engine speed down to 1600 rpm, which is peak engine torque.
Operator visibility and control of operation
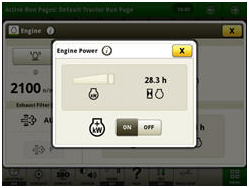
All tractors have the power meter display function as base equipment. The operator can observe when full capabilities of the tractor are being utilized. This function graphically displays power utilization up to rated horsepower and power bulge.
The power meter can be found in the CommandCenter™ display. If the engine is off or has minimal load, the power meter will not fill in. The meter is similar in concept to a cellular phone's signal-strength meter. As the power increases, it will fill in bars in an icon. The display will also show the level of additional power being used. The long section represents up to the rated power. The smaller section represents power bulge and is an indicator of additional power available with IPM.
Via the CommandCenter, there is also the ability to enable or disable the function. The Operator's Manual provides simple details about navigating the engine screen.
If equipped with this option, IPM is automatically enabled each time the tractor is started. IPM can be turned off through the CommandCenter display.
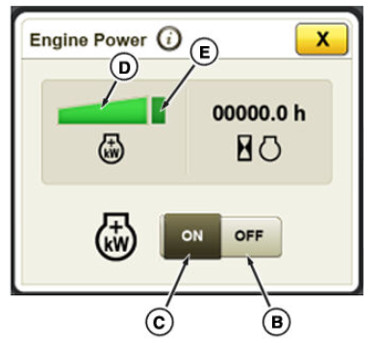
Tractor compatibility with additional power
IPM has been thoroughly tested by John Deere engineers to be compatible with the base tractor equipment with no impact to reliability. John Deere provides IPM. Unapproved aftermarket devices that boost power without regard to engine, transmission, axles, and drawbar, or hitch capability.
This feature provides optimal utilization of tractor components. For example, with moving PTO operation, power splits through axles to move the tractor along the ground and turn the PTO shaft and implement. Adding power to this combined system does not overload either one individually. At transport speeds, axle torque load decreases significantly from levels seen at working field speeds. Adding IPM power at transport does not overload transmissions or axles.
Aftermarket devices are not selective when power increases are available. Great amounts of power increase may be promised with these devices. Large power changes are not compatible with base tractor equipment. The tractor’s systems are specifically designed to ensure durability of the total vehicle as power increases. Operating outside of the design capabilities of the tractor base equipment will have an impact on durability and reliability.
Front Hitch
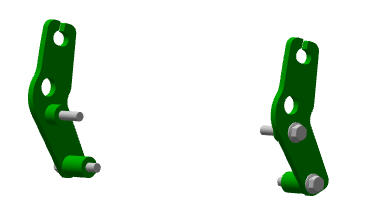
8R Tractors with a factory-installed front hitch do not have position sensing. Due to front hitch implements (like the 131 Mower-Conditioner) being further ahead of the 8R front axle, the front hitch should be operated in the float position. A front hitch chain-hook kit should be installed to control the hitch height position. This kit allows the front hitch to float in the event the suspension reaches its maximum travel.
LAFORGE is a trademark of LAFORGE Corporation.


The front hitch/PTO ready option is ideal for any 7R Tractor that may be used for future applications requiring a front hitch or PTO. This option is also beneficial for increased resale value as it provides flexibility for future owners.
This option includes a front casting that accommodates but does not include a front hitch and front PTO.
- With a mechanical front-wheel drive (MFWD) axle, this option includes one set of hydraulic oil lines to connect the front hitch and mid-mount selective control valve (SCV). Mid-mount valves must be purchased separately. Additional hydraulic lines can be field installed allowing up to two front auxiliary couplers with a John Deere field-installed hitch.
- On tractors with a Triple-Link Suspension (TLS™) front axle, the option includes three sets of hydraulic lines to connect the front hitch to the mid-mount SCV and up to two front auxiliary couplers. Mid-mount valves must be purchased separately.
In-cab controls for front PTO and front hitch must be ordered through Parts when ordering the front PTO and front hitch field-installed options.
Front hitch ready tractors are not shipped with standard front weight support. A front weight support that bolts to the tractor can be ordered as a factory- or field-installed option. The weight support is compatible with suitcase weights (up to 24) and with the 900-kg or 1150-kg (1984-lb or 2535-lb) monster pick-up (monster) weights.
Front weight support is not compatible with front hitch and must be removed before a hitch can be installed.
The sixth rear electrohydraulic SCV is not compatible with front hitch options because of the mid-mount hydraulics for front hitch.
Field-installed hitch options for front hitch/PTO ready tractors:
- Premium (ground-engaging) front hitch with push bar
- Standard (carrier version) front hitch less push bar
Attachments, front-hitch conversion to ground-engaging 5194-kg (11,450-lb) lift capacity
Conversion from carrier version 5194-kg (11,450-lb) lift capacity to ground-engaging 5194-kg (11,450-lb) lift capacity for 7R Tractors
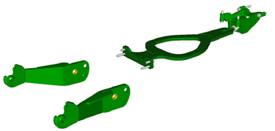
Those who want more productivity out of the 7R Tractors with a carrier-version front hitch can add tillage and other ground-engaging implements with the front-hitch conversion kit. The heavy-duty front hitch is recommended for the most demanding applications. It is designed for extreme stress from pushing hard on tillage implements, very wide implements, severe shock loads, or other heavy-duty applications. Premium hitches are also well suited for mounting three-point blades.
Field-installed kit RE326580 provides a set of heavy-duty lower hitch links, a push bar, and push bar mounting bracket. This hitch is suitable for use under normal conditions including primary tillage equipment or lifting heavy implements. The ground-engaging version is designed for full clearance and does not limit the turning radius at any tread width setting.
The tractor frame includes the mounting points for the push bar, making field conversion possible. Link conversion is possible by removing two pins for each link. Install the push bar with four cap screws in the front, four in the mid-chassis, and tighten two large jam nuts where the push bar attaches to the push bar bracket. There are no ground clearance trade-offs with the addition of the push bar and heavy-duty links. Both versions of the front hitch are entirely compatible with the front power take-off (PTO).
The conversion kit to ground-engaging front hitch adds 117 kg (260 lb) of additional weight to the tractor.


The front hitch/PTO ready option is ideal for any 7R Tractor that may be used for future applications requiring a front hitch or PTO. This option is also beneficial for increased resale value as it provides flexibility for future owners.
This option includes a front casting that accommodates but does not include a front hitch and front PTO.
- With a mechanical front-wheel drive (MFWD) axle, this option includes one set of hydraulic oil lines to connect the front hitch and mid-mount selective control valve (SCV). Mid-mount valves must be purchased separately. Additional hydraulic lines can be field installed allowing up to two front auxiliary couplers with a John Deere field-installed hitch.
- On tractors with a Triple-Link Suspension (TLS™) front axle, the option includes three sets of hydraulic lines to connect the front hitch to the mid-mount SCV and up to two front auxiliary couplers. Mid-mount valves must be purchased separately.
In-cab controls for front PTO and front hitch must be ordered through Parts when ordering the front PTO and front hitch field-installed options.
Front hitch ready tractors are not shipped with standard front weight support. A front weight support that bolts to the tractor can be ordered as a factory- or field-installed option. The weight support is compatible with suitcase weights (up to 24) and with the 900-kg or 1150-kg (1984-lb or 2535-lb) monster pick-up (monster) weights.
Front weight support is not compatible with front hitch and must be removed before a hitch can be installed.
The sixth rear electrohydraulic SCV is not compatible with front hitch options because of the mid-mount hydraulics for front hitch.
Field-installed hitch options for front hitch/PTO ready tractors:
- Premium (ground-engaging) front hitch with push bar
- Standard (carrier version) front hitch less push bar
Attachments, front-hitch conversion to ground-engaging 5194-kg (11,450-lb) lift capacity
Conversion from carrier version 5194-kg (11,450-lb) lift capacity to ground-engaging 5194-kg (11,450-lb) lift capacity for 7R Tractors
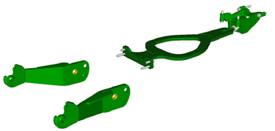
Those who want more productivity out of the 7R Tractors with a carrier-version front hitch can add tillage and other ground-engaging implements with the front-hitch conversion kit. The heavy-duty front hitch is recommended for the most demanding applications. It is designed for extreme stress from pushing hard on tillage implements, very wide implements, severe shock loads, or other heavy-duty applications. Premium hitches are also well suited for mounting three-point blades.
Field-installed kit RE326580 provides a set of heavy-duty lower hitch links, a push bar, and push bar mounting bracket. This hitch is suitable for use under normal conditions including primary tillage equipment or lifting heavy implements. The ground-engaging version is designed for full clearance and does not limit the turning radius at any tread width setting.
The tractor frame includes the mounting points for the push bar, making field conversion possible. Link conversion is possible by removing two pins for each link. Install the push bar with four cap screws in the front, four in the mid-chassis, and tighten two large jam nuts where the push bar attaches to the push bar bracket. There are no ground clearance trade-offs with the addition of the push bar and heavy-duty links. Both versions of the front hitch are entirely compatible with the front power take-off (PTO).
The conversion kit to ground-engaging front hitch adds 117 kg (260 lb) of additional weight to the tractor.
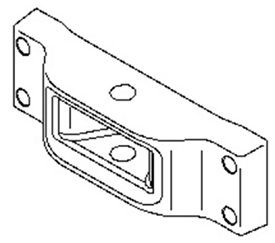
To fulfill the legal requirements of some areas, a front tow point can be field installed on the front base weight. Mounting hardware must be ordered individually.
Front Weights


The front hitch/PTO ready option is ideal for any 7R Tractor that may be used for future applications requiring a front hitch or PTO. This option is also beneficial for increased resale value as it provides flexibility for future owners.
This option includes a front casting that accommodates but does not include a front hitch and front PTO.
- With a mechanical front-wheel drive (MFWD) axle, this option includes one set of hydraulic oil lines to connect the front hitch and mid-mount selective control valve (SCV). Mid-mount valves must be purchased separately. Additional hydraulic lines can be field installed allowing up to two front auxiliary couplers with a John Deere field-installed hitch.
- On tractors with a Triple-Link Suspension (TLS™) front axle, the option includes three sets of hydraulic lines to connect the front hitch to the mid-mount SCV and up to two front auxiliary couplers. Mid-mount valves must be purchased separately.
In-cab controls for front PTO and front hitch must be ordered through Parts when ordering the front PTO and front hitch field-installed options.
Front hitch ready tractors are not shipped with standard front weight support. A front weight support that bolts to the tractor can be ordered as a factory- or field-installed option. The weight support is compatible with suitcase weights (up to 24) and with the 900-kg or 1150-kg (1984-lb or 2535-lb) monster pick-up (monster) weights.
Front weight support is not compatible with front hitch and must be removed before a hitch can be installed.
The sixth rear electrohydraulic SCV is not compatible with front hitch options because of the mid-mount hydraulics for front hitch.
Field-installed hitch options for front hitch/PTO ready tractors:
- Premium (ground-engaging) front hitch with push bar
- Standard (carrier version) front hitch less push bar
Attachments, front-hitch conversion to ground-engaging 5194-kg (11,450-lb) lift capacity
Conversion from carrier version 5194-kg (11,450-lb) lift capacity to ground-engaging 5194-kg (11,450-lb) lift capacity for 7R Tractors
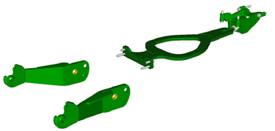
Those who want more productivity out of the 7R Tractors with a carrier-version front hitch can add tillage and other ground-engaging implements with the front-hitch conversion kit. The heavy-duty front hitch is recommended for the most demanding applications. It is designed for extreme stress from pushing hard on tillage implements, very wide implements, severe shock loads, or other heavy-duty applications. Premium hitches are also well suited for mounting three-point blades.
Field-installed kit RE326580 provides a set of heavy-duty lower hitch links, a push bar, and push bar mounting bracket. This hitch is suitable for use under normal conditions including primary tillage equipment or lifting heavy implements. The ground-engaging version is designed for full clearance and does not limit the turning radius at any tread width setting.
The tractor frame includes the mounting points for the push bar, making field conversion possible. Link conversion is possible by removing two pins for each link. Install the push bar with four cap screws in the front, four in the mid-chassis, and tighten two large jam nuts where the push bar attaches to the push bar bracket. There are no ground clearance trade-offs with the addition of the push bar and heavy-duty links. Both versions of the front hitch are entirely compatible with the front power take-off (PTO).
The conversion kit to ground-engaging front hitch adds 117 kg (260 lb) of additional weight to the tractor.
Front weights provide additional ballast for the front axle
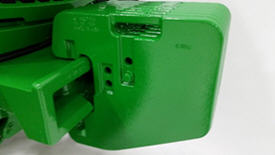
Cast Quik-Tatch suitcase weights (R127764) can be added to provide additional ballast for implements that exert heavy draft loads and require additional ballast or with hitch-mounted implements that require additional ballast to maintain steering control while transporting.
These weights are Quik-Tatch weights that require minimal effort to attach.
Pickup weights
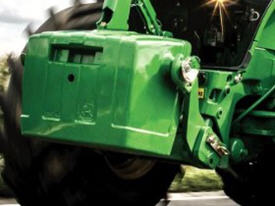
Pickup weights are designed to add fast weight to the tractor. The following pickup weights can be mounted at the front.
Support (base weight):
- 900-kg (1948-lb) pickup weight
- 1150-kg (2535.3-lb) pickup weight
All pickup hitches can also be mounted at the rear in the 3-point hitch as a counter weight. To use the third mounting point, an additional center-link bracket is available.
1500-kg (3307-lb) and 1800-kg (3968.3-lb) pickup weights
The two weights differ only internally, therefore no external differences are visible.
The pickup weights can either be installed on the rear hitch or on the front hitch of the tractor using the center-link bracket. They cannot be mounted directly on the front base weight. A front hitch is required. The center-link bracket for installation is included.
The shape of the 1500-kg (3307-lb) and 1800-kg (3968.3-lb) pick-up weights allows for quick and safe mounting. This is ensured by an optimal alignment of the weight and the tractor along with a self-centering design.
Major benefits of the design:
- Easy and comfortable
- Less time is required
- Lower risk of injury
Due to the user-friendliness, an optimal ballasting of the tractor is guaranteed at any time.
The performance of the tractor is used to a greater extent, which leads to higher productivity and a reduction in fuel consumption.
The weights cannot be front installed in combination with Quik-Tatch front weights.
NOTE: Ballast should be limited by the lowest of either tire capacity or tractor capacity. The carrying capacity of each tire should not be exceeded. For more ballasting information refer to the Operator's Manual and ballast calculator.
Hydraulic Selective Control Valves (SCVs)
This kit is for adding only the SCVs to tractors that are not front hitch ready from the factory.
The addition of these front SCVs are required for the use of front hydraulically-powered implement accessories such as a hitch, loader, snow blower, or other accessories. Additional kits (such as software, mounting brackets, and joysticks) may be necessary depending on the accessory and functionality desired.
This kit is for adding only the SCVs to tractors that are not front hitch ready from the factory.
The addition of these front SCVs are required for the use of front hydraulically-powered implement accessories such as a hitch, loader, snow blower, or other accessories. Additional kits (such as software, mounting brackets, and joysticks) may be necessary depending on the accessory and functionality desired.
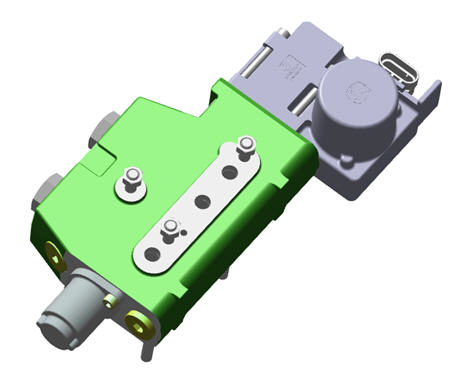
This kit provides additional hydraulic valve control for operation of implements that do not require a front hitch.
It allows for the installation of a third mid-mounted SCV.
This attachment provides SCV hydraulic lines from the mid-valve to the front of the machine to control implement functions from the cab.
This attachment provides SCV hydraulic lines from the mid-valve to the front of the machine to control implement functions from the cab.
Hydraulics
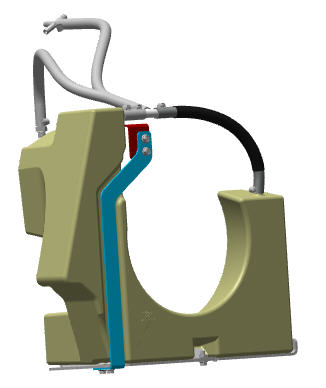

The auxiliary reservoir kit for the 7R Series Tractors holds 20 L (5.3 gal.) of oil, providing a total hydraulic oil capacity of 85 L (22.5 gal.). This additional volume helps ensure that the tractor has enough hydraulic oil for applications using large single-acting cylinders or needing large hydraulic oil flow in a short period of time. Examples of common applications benefiting from the kit are dump wagons, cane carts, and beet or potato harvesters run at lower engine rpm.
The reservoir is only available as a field-installed kit to meet the needs of specific applications and is not needed for ordinary hydraulic operations.
NOTE: CommandQuad™ transmissions have 85 L (22.5 gal.) of takeout standard and do not require this kit.
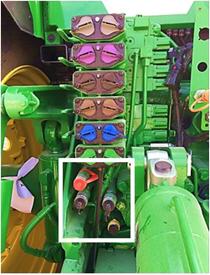
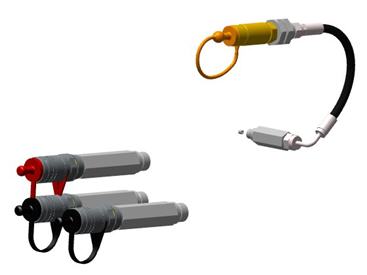
This is a power beyond kit that can be used to assist with hooking up large equipment where multiple connections are required. The function is to supply oil to implements that have their own control valves for certain functions and do not need the controllability aspect that an SCV would give.
The implement single-lever lift-assist kit is designed to be used with implements needing a separate lever to be used for lift-assist wheels.

To assist in hooking up to large equipment requiring multiple connections, various auxiliary hydraulic couplers are available.
This kit includes:
- One load sense coupler
- Two power beyond pressure couplers
- One motor left-return coupler
The components of the kit are suitable for use with most planting and seeding equipment.
Hydraulic motor return couplers can be used as a coupler for return oil flow from hydraulic orbital motors and other devices to the tractor's low-pressure return port, labeled "R" on the tractor.
This connector is used specifically in the return oil from hydraulic components that require a leak-off line connection to the tractor. Components and implements that require this typically are larger, orbital motors that require a drain for seal protection.
The auxiliary sump coupler allows oil to return from the hydraulics motor at low pressures. This coupler is required for correct attachment to current-production seeding products with case drain lines. The connector in the sump port is not to be used to carry return flow from a function to the tractor.
The power beyond coupler provides live hydraulic power to equipment. It supplies oil pressure to implements when the engine is running. Any implement using power beyond must have a way to control oil flow. Use an independent control valves that is a pressure-and-flow-compensating (supplied separately) to control the oil flow rate from this coupler set.
Easy hookup of planters and other implements
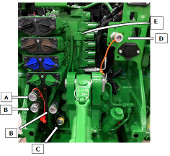
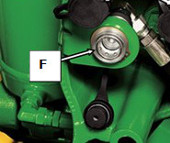
- Pressure port
- Return ports
- Case drain port
- Load sense coupler
- Hitch valve
- Auxiliary hitch valve port (if equipped)
To assist hooking up large equipment where multiple connections are required, factory-installed auxiliary hydraulic couplers are available.
Auxiliary sump coupler
The sump coupler kit allows oil to return from the hydraulics motor at low pressures. This coupler is required for correct attachment to current-production seeding products with case drain lines. The connector in the sump port is not to be used to carry return flow from a function to the tractor.
Hydraulic motor return couplers
The hydraulic motor return couplers can be used as couplers for return oil flow, from hydraulic orbital motors and other devices to the tractor's low-pressure return port, labeled R on the tractor.
Use of this connector specifically in the return to sump port position is for hydraulic components that require a leak-off line connection to the tractor. Components and implements that require this typically are larger orbital motors that require a drain for seal protection. The connector in the sump port is not to be used to carry return flow from a function to the tractor.
Power beyond couplers
Power beyond provides live hydraulic power to equipment. This kit supplies oil pressure to implements when the engine is running.
Any implement using power beyond must have a way to control oil flow. Use an independent control valve that is pressure-and-flow compensating (supplied separately) to control the oil flow rate from this coupler set. Power-beyond functions require a load-sense signal to regulate pump pressure, therefore, a load-sense hydraulic line is used. Certain equipment may require modification.
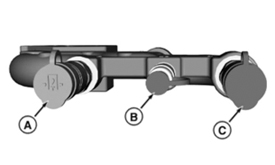
The auxiliary hydraulic optional equipment includes the following:
A – Pressure coupler
B – Load sense coupler
C – Return coupler (motor return)
Easy hookup of planters and other implements
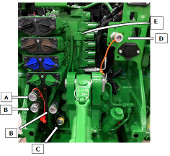
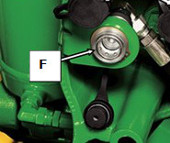
- Pressure port
- Return ports
- Case drain port
- Load sense coupler
- Hitch valve
- Auxiliary hitch valve port (if equipped)
To assist hooking up large equipment where multiple connections are required, factory-installed auxiliary hydraulic couplers are available.
Auxiliary sump coupler
The sump coupler kit allows oil to return from the hydraulics motor at low pressures. This coupler is required for correct attachment to current-production seeding products with case drain lines. The connector in the sump port is not to be used to carry return flow from a function to the tractor.
Hydraulic motor return couplers
The hydraulic motor return couplers can be used as couplers for return oil flow, from hydraulic orbital motors and other devices to the tractor's low-pressure return port, labeled R on the tractor.
Use of this connector specifically in the return to sump port position is for hydraulic components that require a leak-off line connection to the tractor. Components and implements that require this typically are larger orbital motors that require a drain for seal protection. The connector in the sump port is not to be used to carry return flow from a function to the tractor.
Power beyond couplers
Power beyond provides live hydraulic power to equipment. This kit supplies oil pressure to implements when the engine is running.
Any implement using power beyond must have a way to control oil flow. Use an independent control valve that is pressure-and-flow compensating (supplied separately) to control the oil flow rate from this coupler set. Power-beyond functions require a load-sense signal to regulate pump pressure, therefore, a load-sense hydraulic line is used. Certain equipment may require modification.
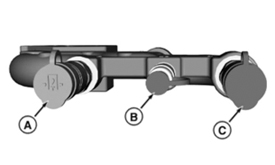
The auxiliary hydraulic optional equipment includes the following:
A – Pressure coupler
B – Load sense coupler
C – Return coupler (motor return)
Easy hookup of planters and other implements
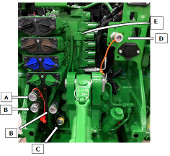
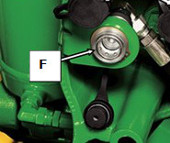
- Pressure port
- Return ports
- Case drain port
- Load sense coupler
- Hitch valve
- Auxiliary hitch valve port (if equipped)
To assist hooking up large equipment where multiple connections are required, factory-installed auxiliary hydraulic couplers are available.
Auxiliary sump coupler
The sump coupler kit allows oil to return from the hydraulics motor at low pressures. This coupler is required for correct attachment to current-production seeding products with case drain lines. The connector in the sump port is not to be used to carry return flow from a function to the tractor.
Hydraulic motor return couplers
The hydraulic motor return couplers can be used as couplers for return oil flow, from hydraulic orbital motors and other devices to the tractor's low-pressure return port, labeled R on the tractor.
Use of this connector specifically in the return to sump port position is for hydraulic components that require a leak-off line connection to the tractor. Components and implements that require this typically are larger orbital motors that require a drain for seal protection. The connector in the sump port is not to be used to carry return flow from a function to the tractor.
Power beyond couplers
Power beyond provides live hydraulic power to equipment. This kit supplies oil pressure to implements when the engine is running.
Any implement using power beyond must have a way to control oil flow. Use an independent control valve that is pressure-and-flow compensating (supplied separately) to control the oil flow rate from this coupler set. Power-beyond functions require a load-sense signal to regulate pump pressure, therefore, a load-sense hydraulic line is used. Certain equipment may require modification.
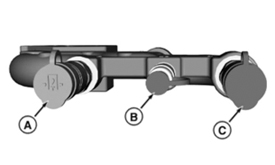
The auxiliary hydraulic optional equipment includes the following:
A – Pressure coupler
B – Load sense coupler
C – Return coupler (motor return)
Lighting

Increase visibility for low light transport and for loader work by adding these lights to the front of the cab at the roofline. Lights are halogen to meet brightness requirements and mount into a fixed position bracket optimized for road use and loader work.
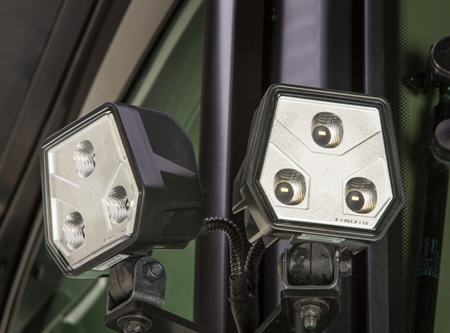
Increase light output over halogen work lights with this four-light kit for the rear corners of the mid-body cab. These lights are the same parts included in the Ultimate Visibility package and are a direct fit upgrade. Each light can be positioned side-to-side and up and down to get the maximum amount of light-emitting diode (LED) light right where it is needed most.

Increase light output over halogen work lights with this four-light kit for the front and rear roof corners of the cab. These lights are the same parts included in the Premium and Ultimate Visibility package and are a plug-and-play update. Eliminate bulb replacements while increasing color temperature and lumen output with this eight-light LED upgrade.
Power Take-Off (PTO)
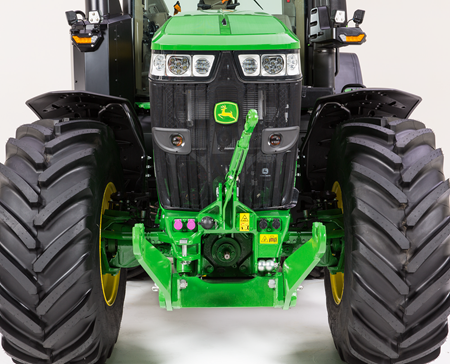
For increased versatility, two 1000-rpm front PTO options are available from the factory for 7R and 8R Series Tractors equipped with the John Deere front hitch.
- Type 2, 1000-rpm (counterclockwise as seen from front), 35-mm (1 3/8-in.), 21-spline front PTO
- Type 3, 1000-rpm (counterclockwise as seen from front), 45-mm (1 ¾-in.) 20-spline front PTO (available through Parts only)
Front PTO features include:
- The ability to be incorporated with iTEC™ sequences
- Three choices of engagement modulation: auto, low, and high
- Integrated controls
- Cornerpost display indicators
- Bolt-on shaft makes it easy to change shafts if necessary.
- Remote PTO engagement
7R specific features:
- 130 kW (175 hp)
- Integrated with all transmissions
- PTO disconnect for efficiency
- Requires Triple-Link Suspension (TLS™) front axle
8R specific features:
- 112 kW (150 hp)
- Integrated with the infinitely variable transmission (IVT™)
- Requires Independent-Link Suspension (ILS™) with front brakes
Intelligent Power Management (IPM)
IPM is compatible with 7R and 8R Series Tractors equipped with a front PTO option. The front PTO, rear PTO, or transport speeds can activate IPM on 7R Tractors. However, on 8R Tractors, IPM is only activated by the rear PTO or by transport speeds. For example:
- A front snow blower will not benefit from IPM on an 8R since the front PTO alone will not activate IPM.
- A triple-mounted mower-conditioner will benefit from IPM as high power levels are transmitted via the rear PTO. The front mower-conditioner will have 112 kW (150 hp) available to it on an 8R, which is adequate to operate these mowers in most crop conditions.
- See Intelligent Power Management for more information.
PTO disconnect on 7 Family Tractors
Disconnecting the PTO drive to the PTO box when not in use increases tractor efficiency by reducing:
- Power requirements, which saves nearly 70 percent of power required to run the PTO disengaged
- Wear on components of the PTO box; components are not moving when the PTO is disconnected
Refer to the Operator’s Manual for instructions on how to disconnect the PTO when not in operation.
Front PTO operation
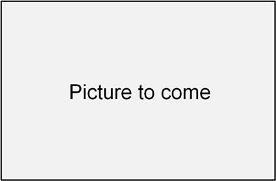
Front PTO engagement is actuated through an engagement switch similar to the rear PTO located on the CommandARM™ controls.
- PTO clutch is electronically activated with automatic torque modulation.
- PTO modulation is selectable through the CommandCenter™ display.
- To activate the PTO remotely, select the remote PTO enable button in Generation 4 CommandCenter display, push down and forward on the front PTO switch in the cab and use the remote control at the front of the tractor.
NOTE: For the 8R Series, if the tractor is equipped with a front PTO, additional IPM power will transfer through the front PTO. However, IPM activation is only sensed through the rear PTO. Adequate load must be sensed on the rear PTO in order for IPM to activate.
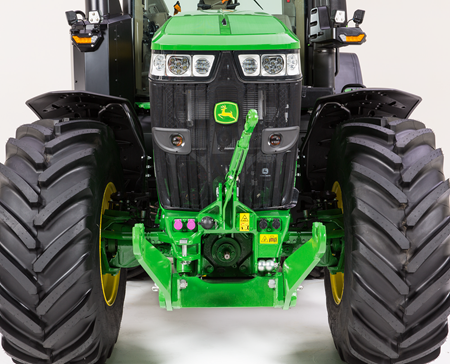
For increased versatility, two 1000-rpm front PTO options are available from the factory for 7R and 8R Series Tractors equipped with the John Deere front hitch.
- Type 2, 1000-rpm (counterclockwise as seen from front), 35-mm (1 3/8-in.), 21-spline front PTO
- Type 3, 1000-rpm (counterclockwise as seen from front), 45-mm (1 ¾-in.) 20-spline front PTO (available through Parts only)
Front PTO features include:
- The ability to be incorporated with iTEC™ sequences
- Three choices of engagement modulation: auto, low, and high
- Integrated controls
- Cornerpost display indicators
- Bolt-on shaft makes it easy to change shafts if necessary.
- Remote PTO engagement
7R specific features:
- 130 kW (175 hp)
- Integrated with all transmissions
- PTO disconnect for efficiency
- Requires Triple-Link Suspension (TLS™) front axle
8R specific features:
- 112 kW (150 hp)
- Integrated with the infinitely variable transmission (IVT™)
- Requires Independent-Link Suspension (ILS™) with front brakes
Intelligent Power Management (IPM)
IPM is compatible with 7R and 8R Series Tractors equipped with a front PTO option. The front PTO, rear PTO, or transport speeds can activate IPM on 7R Tractors. However, on 8R Tractors, IPM is only activated by the rear PTO or by transport speeds. For example:
- A front snow blower will not benefit from IPM on an 8R since the front PTO alone will not activate IPM.
- A triple-mounted mower-conditioner will benefit from IPM as high power levels are transmitted via the rear PTO. The front mower-conditioner will have 112 kW (150 hp) available to it on an 8R, which is adequate to operate these mowers in most crop conditions.
- See Intelligent Power Management for more information.
PTO disconnect on 7 Family Tractors
Disconnecting the PTO drive to the PTO box when not in use increases tractor efficiency by reducing:
- Power requirements, which saves nearly 70 percent of power required to run the PTO disengaged
- Wear on components of the PTO box; components are not moving when the PTO is disconnected
Refer to the Operator’s Manual for instructions on how to disconnect the PTO when not in operation.
Front PTO operation
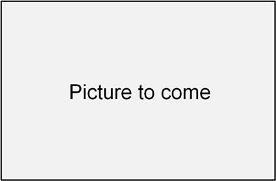
Front PTO engagement is actuated through an engagement switch similar to the rear PTO located on the CommandARM™ controls.
- PTO clutch is electronically activated with automatic torque modulation.
- PTO modulation is selectable through the CommandCenter™ display.
- To activate the PTO remotely, select the remote PTO enable button in Generation 4 CommandCenter display, push down and forward on the front PTO switch in the cab and use the remote control at the front of the tractor.
NOTE: For the 8R Series, if the tractor is equipped with a front PTO, additional IPM power will transfer through the front PTO. However, IPM activation is only sensed through the rear PTO. Adequate load must be sensed on the rear PTO in order for IPM to activate.
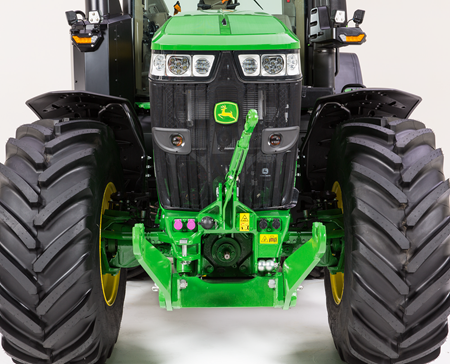
For increased versatility, two 1000-rpm front PTO options are available from the factory for 7R and 8R Series Tractors equipped with the John Deere front hitch.
- Type 2, 1000-rpm (counterclockwise as seen from front), 35-mm (1 3/8-in.), 21-spline front PTO
- Type 3, 1000-rpm (counterclockwise as seen from front), 45-mm (1 ¾-in.) 20-spline front PTO (available through Parts only)
Front PTO features include:
- The ability to be incorporated with iTEC™ sequences
- Three choices of engagement modulation: auto, low, and high
- Integrated controls
- Cornerpost display indicators
- Bolt-on shaft makes it easy to change shafts if necessary.
- Remote PTO engagement
7R specific features:
- 130 kW (175 hp)
- Integrated with all transmissions
- PTO disconnect for efficiency
- Requires Triple-Link Suspension (TLS™) front axle
8R specific features:
- 112 kW (150 hp)
- Integrated with the infinitely variable transmission (IVT™)
- Requires Independent-Link Suspension (ILS™) with front brakes
Intelligent Power Management (IPM)
IPM is compatible with 7R and 8R Series Tractors equipped with a front PTO option. The front PTO, rear PTO, or transport speeds can activate IPM on 7R Tractors. However, on 8R Tractors, IPM is only activated by the rear PTO or by transport speeds. For example:
- A front snow blower will not benefit from IPM on an 8R since the front PTO alone will not activate IPM.
- A triple-mounted mower-conditioner will benefit from IPM as high power levels are transmitted via the rear PTO. The front mower-conditioner will have 112 kW (150 hp) available to it on an 8R, which is adequate to operate these mowers in most crop conditions.
- See Intelligent Power Management for more information.
PTO disconnect on 7 Family Tractors
Disconnecting the PTO drive to the PTO box when not in use increases tractor efficiency by reducing:
- Power requirements, which saves nearly 70 percent of power required to run the PTO disengaged
- Wear on components of the PTO box; components are not moving when the PTO is disconnected
Refer to the Operator’s Manual for instructions on how to disconnect the PTO when not in operation.
Front PTO operation
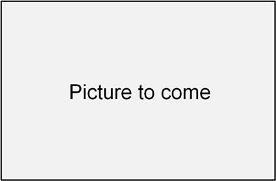
Front PTO engagement is actuated through an engagement switch similar to the rear PTO located on the CommandARM™ controls.
- PTO clutch is electronically activated with automatic torque modulation.
- PTO modulation is selectable through the CommandCenter™ display.
- To activate the PTO remotely, select the remote PTO enable button in Generation 4 CommandCenter display, push down and forward on the front PTO switch in the cab and use the remote control at the front of the tractor.
NOTE: For the 8R Series, if the tractor is equipped with a front PTO, additional IPM power will transfer through the front PTO. However, IPM activation is only sensed through the rear PTO. Adequate load must be sensed on the rear PTO in order for IPM to activate.
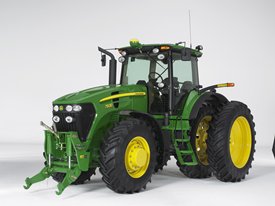
Radio
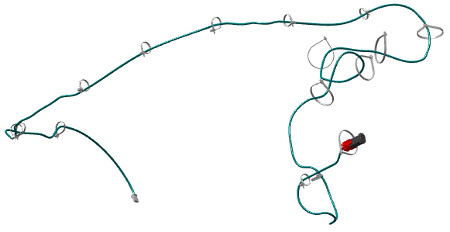
Add video capability to the touchscreen radio by adding this cable (video camera purchased separately). When installed, this cable connection port will be located on the outside of the rear cab next to the factory-installed video connection ports used with the Gen 4 display.
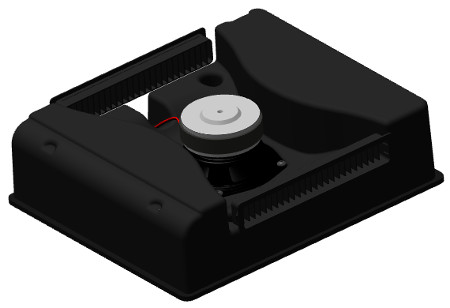
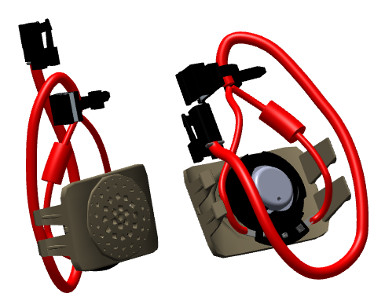
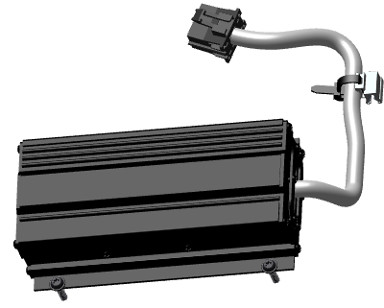
Add deep lows and bright high notes to the cab with this sound kit for the Select cab package radios (single DIN radio style). These components are the same factory-installed speakers that come with the touchscreen radio in the Premium and Ultimate cab packages, but are bundled together in this convenient kit for a Delphi radio.
The subwoofer is mounted under the operator seat, tweeters are added into the front windshield cab frame (after removing the existing plastic inserts), and an amplifier is positioned under the headliner. The entire kit plugs into the existing cab harness and does not need software to activate.
Rear Fenders
Tractors are equipped from the factory with mud guards to keep the left-side steps protected from debris thrown from tire rotation, as well as providing a grab handle to assist entering/exiting the cab. If changing to a different fender coverage size, a matching mud guard will need to be installed using the existing hardware. Order based on fender size.
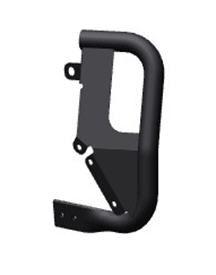
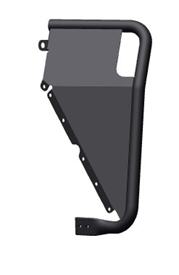


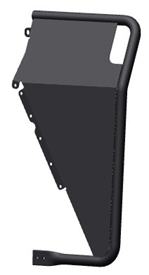
Tractors are equipped from the factory with mud guards to keep the left-side steps protected from debris thrown from tire rotation, as well as providing a grab handle to assist entering/exiting the cab. If changing to a different fender coverage size, a matching mud guard will need to be installed using the existing hardware. Order based on fender size.
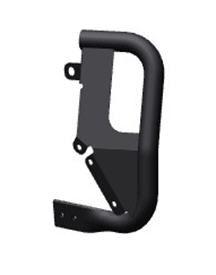
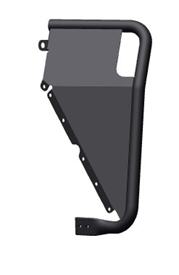


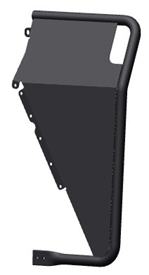
Tractors are equipped from the factory with mud guards to keep the left-side steps protected from debris thrown from tire rotation, as well as providing a grab handle to assist entering/exiting the cab. If changing to a different fender coverage size, a matching mud guard will need to be installed using the existing hardware. Order based on fender size.
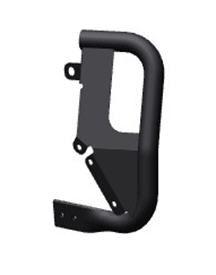
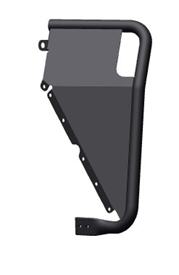


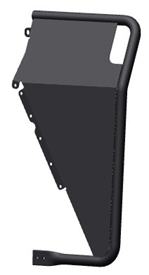
Rear Hitch

To fulfill the hitch equipment demands of producers, a three-in-one hitch can be installed. Additional wagon hitches, like an automatic wagon hitch, a piton-fix hitch, and ball-type hitches, are available to connect to the hitch rails for quick installation and removal, as well as simple, tool-less height adjustments within the rails.

The manual drawbar support works with the three-in-one rail system by attaching a short drawbar accessory. The design works with both Category 3 and 4 drawbars and drawbar pins (ordered separately).
![RE333545 forced steering hitch kit (50-mm [2-in.] ball)](https://salesmanual.deere.com/sales/salesmanual/images/NA/tractors/features_attachment/8_series/re333545_hitch_ball.jpg)
This kit provides a forced steering option for the three-in-one rail hitch.
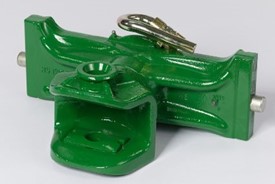
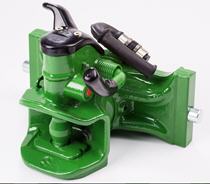
Overview
The manual wagon hitch with 30-mm (1.18-in.) pin will insert into the hitch bracket without the use of tools.
Benefits:
- Hitch exchange without any tools
- Excellent driving comfort and easy coupling
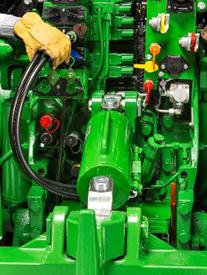
The rear hydraulic center link helps to ease the installation of hitch-mounted implements and makes fine adjustment of the top link effortless.
Center link adjustments can be made in the field by using the control for the third selective control valve (SCV) or from the CommandCenter™ display. Adjustments may also be made using external controls on the rear fenders.
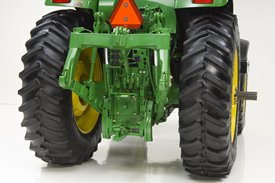
Rear hitch Quik-Coupler kit compatible with 8X30, 7X00, 8X00, 8X00T, 7610, 7710, 7810, 8X10, 8X10T, 8X20, 8X20T, 7X20, 7X30, 6170R, 6190R, 6210R, 6140R, 6150R, 8R, 8RT, and 7R Series Tractors.
Category 3/3N rear rockshaft and hitch with adjustable drawbar, to be installed on tractors ordered less rockshaft.
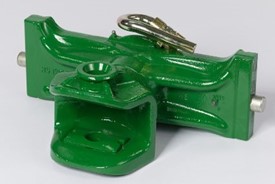
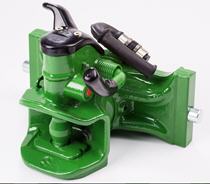
Overview
The manual wagon hitch with 30-mm (1.18-in.) pin will insert into the hitch bracket without the use of tools.
Benefits:
- Hitch exchange without any tools
- Excellent driving comfort and easy coupling
Transmission
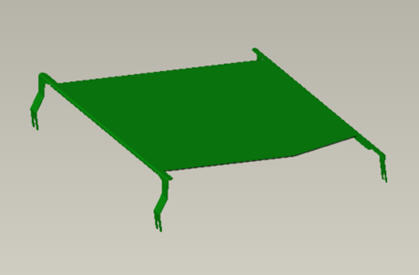
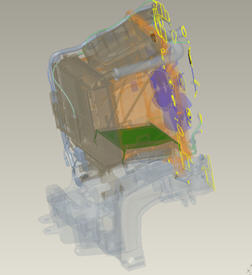
Overview
The hydraulic screen kit is available to protect the cooler from chaff and debris accumulation. Once the kit is installed, the rail system of the kit holds a mesh screen in place at the bottom of the machine. The screen can be easily removed/reinstalled by sliding it through the rails using the service handle.
Benefits
- Minimizes chaff introduction to hydraulic cooler fins
- Reduces cleaning time for cooling components
- Increases the efficiency of the cooler over time (assuming buildup of material is removed from the screen)
The undercarriage crop shield kit is used to protect the undercarriage when working in crops where undercarriage damage is a concern such as in sugar cane or cotton. The undercarriage crop shield protects the transmission and wiring harness on the bottom side of the tractor.
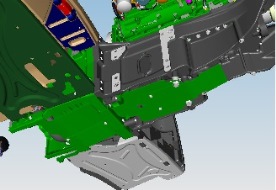
The kit contains four shields and appropriate hardware to install between the front and rear axles and below the fuel tank. The shields are mounted on the bottom side of the chassis (transmission housing casting and oil pan) using existing tapped hole locations.
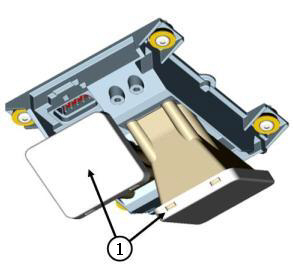
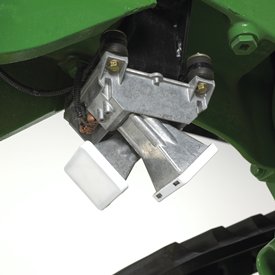
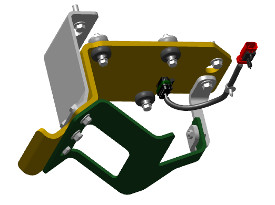
In today’s agricultural environment, accuracy and precision are more important than ever. For something as basic as ground speed, operators need key information for precise control of various implements and the tractor. To support these needs, tractors can be ordered with a dual-beam radar unit as a factory- or field-installed option.
There are several key features that have changed from previous designs.
First, there are two horns for exit of the radio beam. This dual-beam design assures a powerful and accurate signal that will cut through interference that at times makes single-beam units inaccurate (see 1 in the image above for beam locations). Dual-beam output makes radar less susceptible to hard surface or tall/wavy grass interference.
Accuracy is aided by a heavy-gauge mounting bracket and rubber isolators that reduce chances that vibration can affect the radio signal.
Dual-beam radar has a fast update rate. When the tractor comes to a stop, accelerates, or varies speed, the indicated ground speed on the tractor display will closely match the actual ground speed. This is important for implements that use radar speed to control operation such as planters, seeders, fertilizer applicators, and sprayers.
In addition, the dual-beam radar does not require calibration to assure accuracy. Its self-calibrating ability is sure to save setup time by elimination of a special procedure that was required in the past.
The radar true ground speed sensor activates the following CommandCenter™ display or performance monitor readouts:
- Percent slip
- Hitch slip command (if equipped)
Radar usage improves the accuracy of the following CommandCenter display or performance monitor functions:
- Area covered
- Area/hour
- Distance and ground speed
Dual-beam units are compatible with controller area network (CAN) bus and International Organization for Standardization (ISO) bus electrical systems.
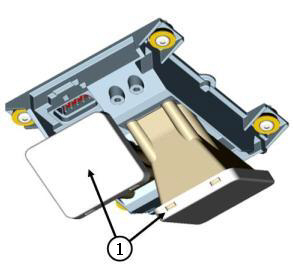
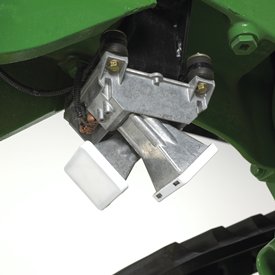
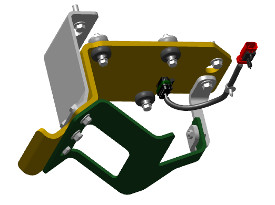
In today’s agricultural environment, accuracy and precision are more important than ever. For something as basic as ground speed, operators need key information for precise control of various implements and the tractor. To support these needs, tractors can be ordered with a dual-beam radar unit as a factory- or field-installed option.
There are several key features that have changed from previous designs.
First, there are two horns for exit of the radio beam. This dual-beam design assures a powerful and accurate signal that will cut through interference that at times makes single-beam units inaccurate (see 1 in the image above for beam locations). Dual-beam output makes radar less susceptible to hard surface or tall/wavy grass interference.
Accuracy is aided by a heavy-gauge mounting bracket and rubber isolators that reduce chances that vibration can affect the radio signal.
Dual-beam radar has a fast update rate. When the tractor comes to a stop, accelerates, or varies speed, the indicated ground speed on the tractor display will closely match the actual ground speed. This is important for implements that use radar speed to control operation such as planters, seeders, fertilizer applicators, and sprayers.
In addition, the dual-beam radar does not require calibration to assure accuracy. Its self-calibrating ability is sure to save setup time by elimination of a special procedure that was required in the past.
The radar true ground speed sensor activates the following CommandCenter™ display or performance monitor readouts:
- Percent slip
- Hitch slip command (if equipped)
Radar usage improves the accuracy of the following CommandCenter display or performance monitor functions:
- Area covered
- Area/hour
- Distance and ground speed
Dual-beam units are compatible with controller area network (CAN) bus and International Organization for Standardization (ISO) bus electrical systems.
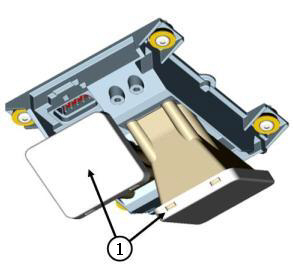
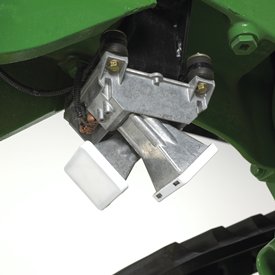
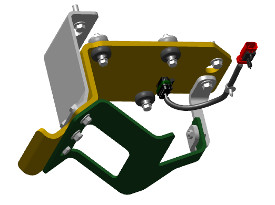
In today’s agricultural environment, accuracy and precision are more important than ever. For something as basic as ground speed, operators need key information for precise control of various implements and the tractor. To support these needs, tractors can be ordered with a dual-beam radar unit as a factory- or field-installed option.
There are several key features that have changed from previous designs.
First, there are two horns for exit of the radio beam. This dual-beam design assures a powerful and accurate signal that will cut through interference that at times makes single-beam units inaccurate (see 1 in the image above for beam locations). Dual-beam output makes radar less susceptible to hard surface or tall/wavy grass interference.
Accuracy is aided by a heavy-gauge mounting bracket and rubber isolators that reduce chances that vibration can affect the radio signal.
Dual-beam radar has a fast update rate. When the tractor comes to a stop, accelerates, or varies speed, the indicated ground speed on the tractor display will closely match the actual ground speed. This is important for implements that use radar speed to control operation such as planters, seeders, fertilizer applicators, and sprayers.
In addition, the dual-beam radar does not require calibration to assure accuracy. Its self-calibrating ability is sure to save setup time by elimination of a special procedure that was required in the past.
The radar true ground speed sensor activates the following CommandCenter™ display or performance monitor readouts:
- Percent slip
- Hitch slip command (if equipped)
Radar usage improves the accuracy of the following CommandCenter display or performance monitor functions:
- Area covered
- Area/hour
- Distance and ground speed
Dual-beam units are compatible with controller area network (CAN) bus and International Organization for Standardization (ISO) bus electrical systems.
Weights
Front weights provide additional ballast for the front axle
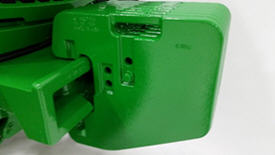
Cast Quik-Tatch suitcase weights (R127764) can be added to provide additional ballast for implements that exert heavy draft loads and require additional ballast or with hitch-mounted implements that require additional ballast to maintain steering control while transporting.
These weights are Quik-Tatch weights that require minimal effort to attach.
Pickup weights
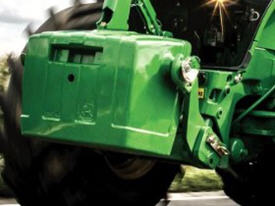
Pickup weights are designed to add fast weight to the tractor. The following pickup weights can be mounted at the front.
Support (base weight):
- 900-kg (1948-lb) pickup weight
- 1150-kg (2535.3-lb) pickup weight
All pickup hitches can also be mounted at the rear in the 3-point hitch as a counter weight. To use the third mounting point, an additional center-link bracket is available.
1500-kg (3307-lb) and 1800-kg (3968.3-lb) pickup weights
The two weights differ only internally, therefore no external differences are visible.
The pickup weights can either be installed on the rear hitch or on the front hitch of the tractor using the center-link bracket. They cannot be mounted directly on the front base weight. A front hitch is required. The center-link bracket for installation is included.
The shape of the 1500-kg (3307-lb) and 1800-kg (3968.3-lb) pick-up weights allows for quick and safe mounting. This is ensured by an optimal alignment of the weight and the tractor along with a self-centering design.
Major benefits of the design:
- Easy and comfortable
- Less time is required
- Lower risk of injury
Due to the user-friendliness, an optimal ballasting of the tractor is guaranteed at any time.
The performance of the tractor is used to a greater extent, which leads to higher productivity and a reduction in fuel consumption.
The weights cannot be front installed in combination with Quik-Tatch front weights.
NOTE: Ballast should be limited by the lowest of either tire capacity or tractor capacity. The carrying capacity of each tire should not be exceeded. For more ballasting information refer to the Operator's Manual and ballast calculator.
Front weights provide additional ballast for the front axle
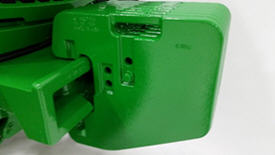
Cast Quik-Tatch suitcase weights (R127764) can be added to provide additional ballast for implements that exert heavy draft loads and require additional ballast or with hitch-mounted implements that require additional ballast to maintain steering control while transporting.
These weights are Quik-Tatch weights that require minimal effort to attach.
Pickup weights
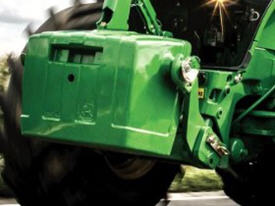
Pickup weights are designed to add fast weight to the tractor. The following pickup weights can be mounted at the front.
Support (base weight):
- 900-kg (1948-lb) pickup weight
- 1150-kg (2535.3-lb) pickup weight
All pickup hitches can also be mounted at the rear in the 3-point hitch as a counter weight. To use the third mounting point, an additional center-link bracket is available.
1500-kg (3307-lb) and 1800-kg (3968.3-lb) pickup weights
The two weights differ only internally, therefore no external differences are visible.
The pickup weights can either be installed on the rear hitch or on the front hitch of the tractor using the center-link bracket. They cannot be mounted directly on the front base weight. A front hitch is required. The center-link bracket for installation is included.
The shape of the 1500-kg (3307-lb) and 1800-kg (3968.3-lb) pick-up weights allows for quick and safe mounting. This is ensured by an optimal alignment of the weight and the tractor along with a self-centering design.
Major benefits of the design:
- Easy and comfortable
- Less time is required
- Lower risk of injury
Due to the user-friendliness, an optimal ballasting of the tractor is guaranteed at any time.
The performance of the tractor is used to a greater extent, which leads to higher productivity and a reduction in fuel consumption.
The weights cannot be front installed in combination with Quik-Tatch front weights.
NOTE: Ballast should be limited by the lowest of either tire capacity or tractor capacity. The carrying capacity of each tire should not be exceeded. For more ballasting information refer to the Operator's Manual and ballast calculator.
Wheel Weights
For operators requiring additional ballast or additional traction on the rear axle
72-kg (159-lb), 205-kg (452-lb), 625-kg (1378-lb), and 970-kg (2138-lb) cast rear-wheel weights are available for the 7R and 8R Tractors. The attaching hardware for all rear-wheel weight options may be ordered through parts.
The range of rear-wheel weights can provide the proper amount of rear axle ballast for a variety of applications. The addition of this ballast will increase traction on the rear axle of the tractor. These weights can also be used to counterbalance the effect of adding additional weight on the front axle in the form of a front weight support, front hitch, front spray tanks, and front-end loaders.
205-kg (452-lb) weight
The 205-kg (452-lb) cast rear-wheel weight is offered individually as attachment R07782. The 72-kg (159-lb) starter weight (R167153) must be installed prior to the 205-kg (452-lb) weight on rear steel wheels. This practice is optional on cast wheels; however, most weight packages will be configured this way.
625-kg (1378-lb) weight
R553540 includes one 625-kg (1378-lb) cast inner rear-wheel weight. This weight is to be used on the inside of the rear wheel assembly. This option can be stacked on a double-flat cast hub, with a 70-kg (154-lb) starter ring on the outside.
70-kg (154-lb) weight
BRE10026 features a 70-kg (154-lb) starter weight. The starter weight and guide lugs provide improved installation and removal of the 900-kg (1984-lb) weight. This weight can be used individually on the outside of the steel, dual rims on rack-and-pinion axles, or on the outside of the double-flat, single-taper wheel hub. For the approved cast hubs, can also be used with the inner cast weights as well.
NOTE: Use on the outer side of approved cast hubs will limit dual tire and spacing capability.
900-kg (1984-lb) weight
Individual R341378 900-kg (1984-lb) weights ordered through Parts. The 70-kg (154-lb) starter weight is required for installation and provides guide lugs for improved installation and removal of the 900-kg (1984-lb) weight. 900-kg (1984-lb) weight ballast option is compatible with steel, dual wheels with rim diameters of 106.7, 116.8 cm, or 127 cm (42 in., 46 in., or 50 in.). This allows the weights to be added to only the outer rear dual on a rack-and-pinion axle and double-flat axle with single-taper hub.
NOTE: This weight option is not compatible with 96.5-cm or 137.2-cm (38-in. or 54-in.) wheels.
For operators requiring additional ballast or additional traction on the rear axle
72-kg (159-lb), 205-kg (452-lb), 625-kg (1378-lb), and 970-kg (2138-lb) cast rear-wheel weights are available for the 7R and 8R Tractors. The attaching hardware for all rear-wheel weight options may be ordered through parts.
The range of rear-wheel weights can provide the proper amount of rear axle ballast for a variety of applications. The addition of this ballast will increase traction on the rear axle of the tractor. These weights can also be used to counterbalance the effect of adding additional weight on the front axle in the form of a front weight support, front hitch, front spray tanks, and front-end loaders.
205-kg (452-lb) weight
The 205-kg (452-lb) cast rear-wheel weight is offered individually as attachment R07782. The 72-kg (159-lb) starter weight (R167153) must be installed prior to the 205-kg (452-lb) weight on rear steel wheels. This practice is optional on cast wheels; however, most weight packages will be configured this way.
625-kg (1378-lb) weight
R553540 includes one 625-kg (1378-lb) cast inner rear-wheel weight. This weight is to be used on the inside of the rear wheel assembly. This option can be stacked on a double-flat cast hub, with a 70-kg (154-lb) starter ring on the outside.
70-kg (154-lb) weight
BRE10026 features a 70-kg (154-lb) starter weight. The starter weight and guide lugs provide improved installation and removal of the 900-kg (1984-lb) weight. This weight can be used individually on the outside of the steel, dual rims on rack-and-pinion axles, or on the outside of the double-flat, single-taper wheel hub. For the approved cast hubs, can also be used with the inner cast weights as well.
NOTE: Use on the outer side of approved cast hubs will limit dual tire and spacing capability.
900-kg (1984-lb) weight
Individual R341378 900-kg (1984-lb) weights ordered through Parts. The 70-kg (154-lb) starter weight is required for installation and provides guide lugs for improved installation and removal of the 900-kg (1984-lb) weight. 900-kg (1984-lb) weight ballast option is compatible with steel, dual wheels with rim diameters of 106.7, 116.8 cm, or 127 cm (42 in., 46 in., or 50 in.). This allows the weights to be added to only the outer rear dual on a rack-and-pinion axle and double-flat axle with single-taper hub.
NOTE: This weight option is not compatible with 96.5-cm or 137.2-cm (38-in. or 54-in.) wheels.
For operators requiring additional ballast or additional traction on the rear axle
72-kg (159-lb), 205-kg (452-lb), 625-kg (1378-lb), and 970-kg (2138-lb) cast rear-wheel weights are available for the 7R and 8R Tractors. The attaching hardware for all rear-wheel weight options may be ordered through parts.
The range of rear-wheel weights can provide the proper amount of rear axle ballast for a variety of applications. The addition of this ballast will increase traction on the rear axle of the tractor. These weights can also be used to counterbalance the effect of adding additional weight on the front axle in the form of a front weight support, front hitch, front spray tanks, and front-end loaders.
205-kg (452-lb) weight
The 205-kg (452-lb) cast rear-wheel weight is offered individually as attachment R07782. The 72-kg (159-lb) starter weight (R167153) must be installed prior to the 205-kg (452-lb) weight on rear steel wheels. This practice is optional on cast wheels; however, most weight packages will be configured this way.
625-kg (1378-lb) weight
R553540 includes one 625-kg (1378-lb) cast inner rear-wheel weight. This weight is to be used on the inside of the rear wheel assembly. This option can be stacked on a double-flat cast hub, with a 70-kg (154-lb) starter ring on the outside.
70-kg (154-lb) weight
BRE10026 features a 70-kg (154-lb) starter weight. The starter weight and guide lugs provide improved installation and removal of the 900-kg (1984-lb) weight. This weight can be used individually on the outside of the steel, dual rims on rack-and-pinion axles, or on the outside of the double-flat, single-taper wheel hub. For the approved cast hubs, can also be used with the inner cast weights as well.
NOTE: Use on the outer side of approved cast hubs will limit dual tire and spacing capability.
900-kg (1984-lb) weight
Individual R341378 900-kg (1984-lb) weights ordered through Parts. The 70-kg (154-lb) starter weight is required for installation and provides guide lugs for improved installation and removal of the 900-kg (1984-lb) weight. 900-kg (1984-lb) weight ballast option is compatible with steel, dual wheels with rim diameters of 106.7, 116.8 cm, or 127 cm (42 in., 46 in., or 50 in.). This allows the weights to be added to only the outer rear dual on a rack-and-pinion axle and double-flat axle with single-taper hub.
NOTE: This weight option is not compatible with 96.5-cm or 137.2-cm (38-in. or 54-in.) wheels.
For operators requiring additional ballast or additional traction on the rear axle
72-kg (159-lb), 205-kg (452-lb), 625-kg (1378-lb), and 970-kg (2138-lb) cast rear-wheel weights are available for the 7R and 8R Tractors. The attaching hardware for all rear-wheel weight options may be ordered through parts.
The range of rear-wheel weights can provide the proper amount of rear axle ballast for a variety of applications. The addition of this ballast will increase traction on the rear axle of the tractor. These weights can also be used to counterbalance the effect of adding additional weight on the front axle in the form of a front weight support, front hitch, front spray tanks, and front-end loaders.
205-kg (452-lb) weight
The 205-kg (452-lb) cast rear-wheel weight is offered individually as attachment R07782. The 72-kg (159-lb) starter weight (R167153) must be installed prior to the 205-kg (452-lb) weight on rear steel wheels. This practice is optional on cast wheels; however, most weight packages will be configured this way.
625-kg (1378-lb) weight
R553540 includes one 625-kg (1378-lb) cast inner rear-wheel weight. This weight is to be used on the inside of the rear wheel assembly. This option can be stacked on a double-flat cast hub, with a 70-kg (154-lb) starter ring on the outside.
70-kg (154-lb) weight
BRE10026 features a 70-kg (154-lb) starter weight. The starter weight and guide lugs provide improved installation and removal of the 900-kg (1984-lb) weight. This weight can be used individually on the outside of the steel, dual rims on rack-and-pinion axles, or on the outside of the double-flat, single-taper wheel hub. For the approved cast hubs, can also be used with the inner cast weights as well.
NOTE: Use on the outer side of approved cast hubs will limit dual tire and spacing capability.
900-kg (1984-lb) weight
Individual R341378 900-kg (1984-lb) weights ordered through Parts. The 70-kg (154-lb) starter weight is required for installation and provides guide lugs for improved installation and removal of the 900-kg (1984-lb) weight. 900-kg (1984-lb) weight ballast option is compatible with steel, dual wheels with rim diameters of 106.7, 116.8 cm, or 127 cm (42 in., 46 in., or 50 in.). This allows the weights to be added to only the outer rear dual on a rack-and-pinion axle and double-flat axle with single-taper hub.
NOTE: This weight option is not compatible with 96.5-cm or 137.2-cm (38-in. or 54-in.) wheels.
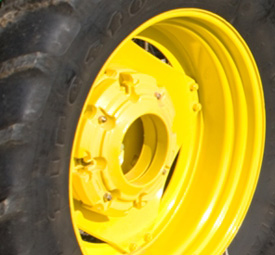

Cast-iron wheel weights provide added ballast at the tires for increased traction and stability.
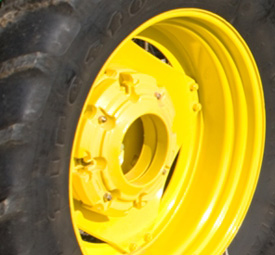

Cast-iron wheel weights provide added ballast at the tires for increased traction and stability.
Wheels and Hubs
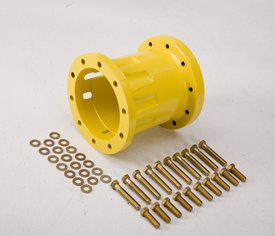
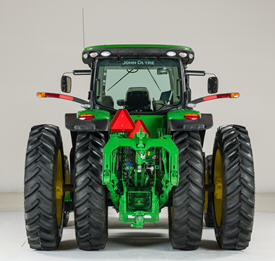
Hub extensions mount to the dual/triple hub to extend the steel wheel tread width for exact dual/triple-wheel spacing for 50.8-cm (20-in.) through 101.6-cm (40-in.) rows.
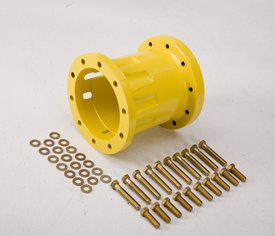
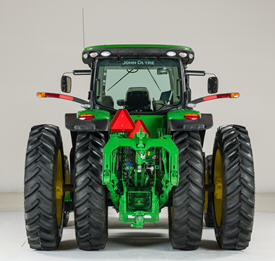
Hub extensions mount to the dual/triple hub to extend the steel wheel tread width for exact dual/triple-wheel spacing for 50.8-cm (20-in.) through 101.6-cm (40-in.) rows.
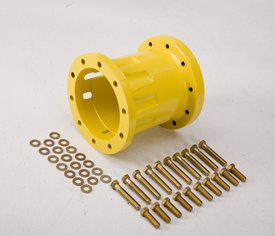
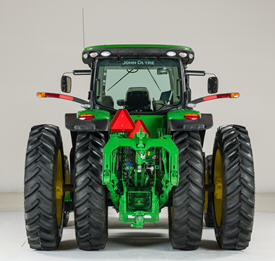
Hub extensions mount to the dual/triple hub to extend the steel wheel tread width for exact dual/triple-wheel spacing for 50.8-cm (20-in.) through 101.6-cm (40-in.) rows.
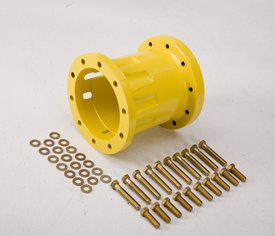
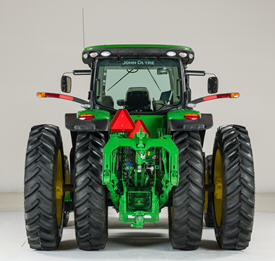
Hub extensions mount to the dual/triple hub to extend the steel wheel tread width for exact dual/triple-wheel spacing for 50.8-cm (20-in.) through 101.6-cm (40-in.) rows.
Videos
© COPYRIGHT 2025 SMITH TRACTOR CO. EQUIPMENT - ALL RIGHTS RESERVED| Privacy Policy | Powered By